Централният електрод е монтиран в канала на изолатора с променлив диаметър. Електродната глава лежи върху коничната повърхност на канала на изолатора в точката на преход от по-голям диаметър към по-малък. Работната част на централния електрод излиза от изолатора с 1,0 до 5,0 mm. Фиксирането на електрода в канала на изолатора и уплътняването на тази връзка се извършва с помощта на стъклен уплътнител. Представлява смес от специално техническо стъкло и метален прах. Стъклото трябва да има коефициент на топлинно разширение, равен на този на керамиката. В този случай уплътнителната тапа няма да бъде разрушена от температурни промени по време на работа. Mogall прах (мед или олово) се добавя към стъклото, за да го направи електропроводимо.
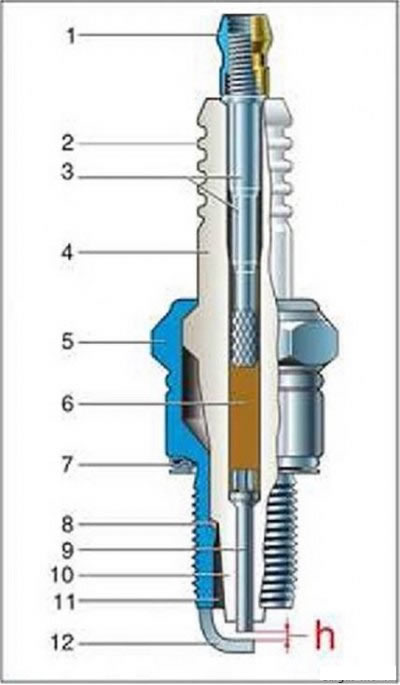
Фиг. 9 - Устройство на запалителната свещ: 1 - контактна гайка: 2 - ребра на изолатора (бариери за патешки ток): 3 - контактен прът: 4 - керамичен изолатор: 5 - метален корпус, b - щепсел от стъклен уплътнител. 7 - уплътнителен кол: 8 - радиаторна шайба: 9 - централен електрод. 10 - термичен конус на изолатора: 11 - работна камера: 12 страничен електрод -маса-: h - искрова междина
Сглобяването на сърцевината (изолаторен монтаж с централния електрод и контактния прът) се извършва в следния ред. Електродът се монтира в канала на изолатора и отгоре се изсипва прахообразен стъклен уплътнител или се поставя под формата на таблетка. След това в канала на изолатора се монтира контактна глава. Преди пресоването стъкленият уплътнител заема по-голям обем, отколкото след тази операция, и контактният прът не може да влезе напълно в канала на изолатора, той стърчи над изолатора с около една трета от дължината. Заготовката се нагрява до температура 700-900 "C и със сила от няколко десетки килограма контактният прът се вкарва в стъкления уплътнител, омекотен под въздействието на температурата. В същото време той се влива в пролуките между изолационния канал, главата на централния електрод и контактната глава.
Ако е необходимо да се вгради електрическо съпротивление във веригата на централния електрод, се използва резистивен стъклен уплътнител за потискане на електромагнитните смущения. След охлаждане уплътнителната тапа придобива електрическо съпротивление с необходимата стойност.
Сърцевината е монтирана в тялото на свещта, така че да влезе в контакт с нейната конична повърхност със съответната повърхност вътре в тялото. Между тези повърхности е монтирана уплътнителна топлоотвеждаща шайба (медна или стоманена).
Фиксирането на сърцевината се извършва чрез навиване на рамото на корпуса върху колана на изолатора. Уплътняването на връзката изолатор - тяло се извършва по метода на разгъване на тялото в нагрято състояние (термореактивно).
Страничният електрод - маса "с правоъгълно сечение е заварен към края на корпуса и огънат към централния. В основата на корпуса е монтиран о-пръстен с акцент върху плоска опорна повърхност, предназначена да уплътни връзката между запалителната свещ и двигателя.
На резбовата част на контактния прът се монтира контактна гайка, ако това се изисква от конструкцията на накрайника на високоволтовия проводник. При някои свещи контактният прът няма глава с резба, той веднага се щампова под формата на контактна гайка.
Изолатор
За да се осигури непрекъснато искрене, изолаторът трябва да има необходимата диелектрична якост дори при високи работни температури. Напрежението, приложено към изолатора по време на работа на двигателя, е равно на напрежението на пробив на искрова междина. Това напрежение се увеличава с увеличаване на налягането и размера на междината и намалява с повишаване на температурата. При двигатели с класическа система за запалване се използват запалителни свещи с искрово разстояние 0,5-0,7 mm. Максималното напрежение на пробив при тези условия не надвишава 12-15 kV (пикова стойност). При двигатели с електронни системи за запалване, инсталационната искра е 0,8-1,0 mm. По време на работа може да се увеличи до 1,3-1,5 мм (и за двете системи). В този случай напрежението на разрушаване може да достигне 20-25 kV.
Дизайнът на изолатора е сравнително прост - това е цилиндър с аксиален отвор за монтиране на централния електрод.
в средната част на изолатора има удебеление, т. нар. "колан" за връзка с тялото. Под пояса има по-тънка цилиндрична част - -дулсе-, преминаваща в термичен конус. В преходната точка от гърлото към термичния конус има конична повърхност, предназначена за монтаж между изолатора и тялото на топлоотвеждащата уплътнителна шайба. Над пояса е разположено -глава', а на прехода от пояса към главата има рамо за навиване на рамото на тялото при сглобяване на свещта.
Допустимо, като се вземе предвид коефициентът на безопасност, дебелината на стената се определя от диелектричната якост на изолационния материал. Според вътрешните стандарти изолаторът трябва да издържа на изпитвателно напрежение от 18 до 22 kV (ефективна стойност), което е 1,4 пъти по-голямо от амплитудата. За повечето автомобилни свещи тази стойност е около 25 mm. По-нататъшното увеличение е неефективно и води до намаляване на механичната якост на изолатора. За да се изключи възможността от електрически пробив по повърхността на изолатора, главата му е снабдена с пръстеновидни канали (токови бариери) и е покрита със специална глазура, за да я предпази от евентуално замърсяване.
Функцията за защита срещу повърхностно припокриване от страната на горивната камера се изпълнява от термичен конус. Тази най-важна част от изолатора, със сравнително малки размери, издържа на горното напрежение, без да се припокрива на повърхността.
Първоначално като изолационен материал се използва обикновен порцелан. но такъв изолатор слабо издържа на топлинни ефекти и има ниска механична якост.
С увеличаване на мощността на двигателя бяха необходими по-надеждни изолатори. отколкото порцелан. Изолаторите от слюда се използват отдавна. Въпреки това, когато се използват горива с добавка на олово, слюдата се унищожава. Изолаторите отново бяха изработени от керамика, но не от порцелан, а от особено издръжлива техническа керамика.
Най-разпространената и икономически изгодна за производството на изолатори е технологията на изостатично пресоване, когато гранулите с необходимия състав и физични свойства се произвеждат от предварително подготвени компоненти. Заготовките на изолаторите се пресоват от гранули при високо налягане, смилат се до необходимите размери, като се вземе предвид свиването по време на изпичане и след това се изпичат веднъж.
Съвременните изолатори са направени от структурна керамика с високо съдържание на алуминий на базата на алуминиев оксид. Такава керамика, съдържаща около 95% алуминиев оксид, е в състояние да издържа на температури до 1600°C и има висока електрическа и механична якост.
Най-важното предимство на алуминиевата керамика е, че има висока топлопроводимост. Това значително подобрява топлинната характеристика на свещта, тъй като основният топлинен поток преминава през изолатора, влизайки в свещта през термичния конус и централния електрод (фиг. 10).
Тяло
Металният корпус е предназначен за монтиране на свещ в двигателя и осигурява плътност на връзката с изолатора. Към края му е заварен страничен електрод, а в конструкциите с пръстеновидна искрова междина тялото директно изпълнява функцията на "земния" електрод.
Тялото е направено чрез щамповане или струговане от конструкционни нисковъглеродни стомани.
вътре в корпуса има пръстеновидна издатина с конична повърхност. върху който лежи изолаторът. Върху цилиндричната част на тялото е направен пръстеновиден жлеб, така нареченият термореактивен жлеб. В процеса на сглобяване на свещта, горното рамо на тялото се навива върху изолационния колан. След това се нагрява и отлага върху преса, докато термореактивният жлеб се подлага на пластична деформация, а тялото плътно покрива изолатора. В резултат на топлинните валежи тялото е в напрегнато състояние, което осигурява херметичността на свещта за целия експлоатационен живот.
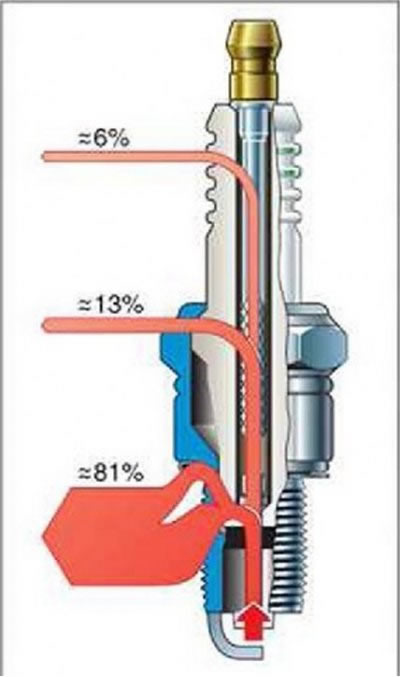
Фиг. 10. Топлинни потоци в изолатора на свещта
Електроди
Както бе споменато по-горе, за да се подобри ефективността на запалването, електродите на запалителната свещ трябва да са възможно най-тънки и дълги, а искровата междина трябва да има максимално допустимата стойност. От друга страна, за да се осигури издръжливост, електродите трябва да са достатъчно масивни.
Следователно, в зависимост от изискванията за мощност, горивна ефективност и токсичност на двигателите, от една страна, и изискванията за издръжливост на запалителната свещ, от друга страна, за всеки тип двигател е разработен отделен дизайн на електроди.
Появата на биметални електроди направи възможно решаването на този проблем до известна степен, тъй като такъв електрод има достатъчна топлопроводимост. За разлика от обичайния "монометален", при работа на двигател той има по-ниска температура и съответно по-дълъг ресурс. В случаите, когато е необходимо да се увеличи ресурсът, се използват два "масови" електрода (фиг. 11). При свещи от чуждестранно производство за тази цел се използват три или дори четири електрода. Местната индустрия произвежда свещи с такъв брой на електроди само за авиационни и промишлени газови двигатели Трябва да се отбележи, че с увеличаване на броя на електродите устойчивостта на въглеродни отлагания намалява и почистването от въглеродни отлагания става по-трудно.
Следните изисквания са наложени на електродния материал: висока устойчивост на корозия и ерозия: устойчивост на топлина и устойчивост на мащаб: висока топлопроводимост; пластичност, достатъчна за щамповане. Цената на материала не трябва да бъде висока, Най-разпространените в местната индустрия за производство на централни електроди на запалителни свещи са топлоустойчиви сплави: желязо-хром-титан, никел-хром-желязо и никел-хром с различни легирания добавки
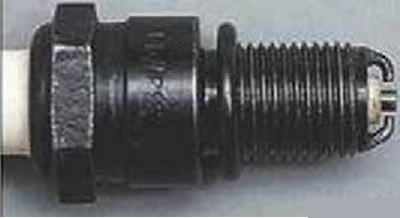
Фиг. 11. Свещ А26ДВ-1 с два заземителни електрода
Страничната електродна "маса" трябва да има висока топлоустойчивост и устойчивост на корозия. Той трябва да има добра заваряемост с обикновена конструкционна стомана, от която е направено тялото, следователно се използва никел-манганова сплав (например NMts-5). Страничният електрод трябва да има добра пластичност, за да може да контролира искрова междина.
За да се намали охлаждащият ефект на електродите, при рафиниране на свещите се правят жлебове върху електродите, а в заземяващия електрод се правят проходни отвори. Понякога страничният електрод се разделя на две части, превръщайки едноелектродна свещ в двуелектродна.
Вграден резистор
Искровият разряд е източник на електромагнитни смущения, включително радиоприемане. За потискането им между централния електрод и контактната глава се монтира резистор с електрическо съпротивление от 4 до 13 kOhm при температура 25±10°C. По време на работа е разрешено да се променя стойността на това съпротивление в диапазона 2-50 kOhm след излагане на температури от -40 до +300°C и импулси с високо напрежение.
Допълнителен изолатор
Дори малките загуби на енергия за запалване водят до отслабване на искрата с всички неприятни последици: влошаване при стартиране, нестабилна работа на празен ход, загуба на мощност на двигателя, прекомерен разход на гориво, повишена токсичност на отработените газове и др. Ако повърхността на изолатора е покрити със сажди, мръсотия или просто влага, има изтичане на ток "към земята". Открива се на тъмно под формата на коронен разряд върху повърхността на изолатора. Изтичането през замърсената повърхност на термичния конус на изолатора в горивната камера на двигателя може да доведе до повреда в искренето. Най-радикалният начин за увеличаване на електрическата якост на изолацията е инсталирането на допълнителен изолатор под формата на керамична втулка между тялото и контактната глава на свещта. Така свещта придобива двойна защита срещу изтичане на ток "на земята".
Предкамерни свещи
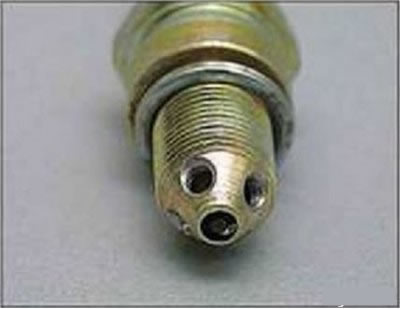
Фиг. 12. Предкамерна свещ
Има различни версии на устройството за свещи, в които работната камера е направена под формата на предкамера. Използват се за подобряване на изгарянето на работната смес. Предкамерните свещи са подобни на свещите за форсирани спортни двигатели, където електродите за защита срещу прегряване са монтирани дълбоко в работната камера на тялото. Разликата е. тази дупка. свързвайки работната камера (предкамера) с цилиндъра на двигателя, направете специална форма. Когато се компресира, свежата смес навлиза в предкамерата, в областта на вихровия поток възниква искров разряд и образуването на първичното място на запалване става по-интензивно. Това осигурява бързо разпространение на пламъка в предкамерата. Налягането се повишава бързо и изхвърля факла от пламък,
Когато горящите газове преминават от предкамерата в цилиндъра на двигателя, поради турбулентността на горимата смес, процесът на горене се ускорява и става по-ефективен. То. от своя страна може да доведе до подобряване на показателите, характеризиращи горивната ефективност и токсичността на отработените газове.
Недостатъците на предкамерните свещи са, че амортизационният ефект на електродите е голям и устойчивостта на въглеродни отлагания е ниска. Вентилацията на предкамерата е затруднена и горимата смес в нея съдържа повишено количество остатъчни газове. Когато горящите газове преминават от предкамерата в цилиндъра, възникват допълнителни топлинни загуби. Един от вариантите на предкамерната свещ е показан на фиг. 12.