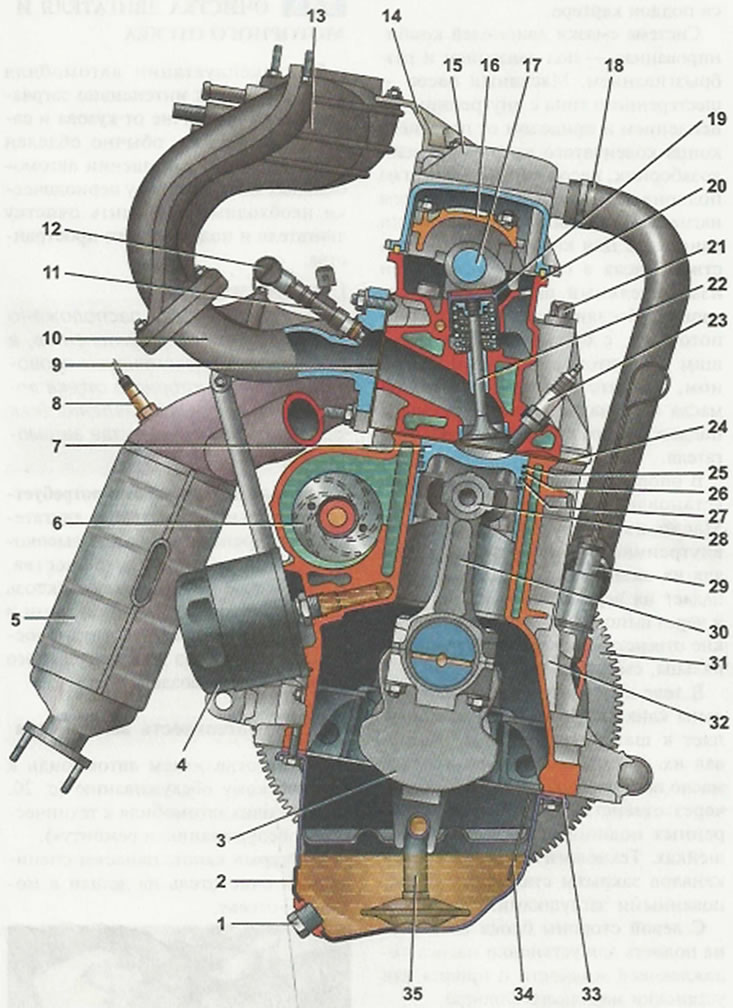
Cross section of the engine: 1 - drain plug of the oil pan; 2 - engine crankcase sump 3 - crankshaft: 4 - oil filter: 5 - catalytic manifold; 6 - coolant pump: 7 - piston; 8 - oxygen concentration sensor: 9 - gasket of the inlet pipeline and exhaust manifold; 10 - inlet pipeline; 11 - nozzle; 12 - diagnostic fitting of the fuel rail; 13 - receiver; 14 - bracket for fastening the tip of the cable sheath; 15 - cylinder head cover; 16 - camshaft bearing housing; 17 - camshaft; 18 - hose of the crankcase ventilation system; 19 - valve pusher; 20 - cylinder head; 21 - a bolt of fastening of a head to the block of cylinders; 22 - valve; 23 - candle; 24 - cylinder head gasket; 25 - top compression ring; 26 - lower compression ring; 27 - oil scraper ring; 28 - piston pin; 29 - fitting for installing an oil level indicator; 30 - connecting rod; 31 - flywheel; 32 - cylinder block; 33 - gasket of the oil pan; 34 - oil level indicator; 35 - oil intake.
Engines - gasoline, four-stroke, four-cylinder in-line with an overhead camshaft and liquid cooling.
Eight-valve engines with a working volume of 1.6 liters are based on the VAZ-2111 engine. They have a cylinder block increased in height by 2.3 mm and an original crankshaft. The cylinder diameter remains the same - 82 mm, the piston stroke is increased to 75.6 mm, in contrast to 71 mm for the base engine. Oil jets are installed in the main bearings.
The cylinder head has one camshaft, eight valves and eight valve lifters with shims. Camshaft bearings completed! in the head. Two camshaft bearing housings are bolted to the upper plane of the head. From above, the gas distribution mechanism is closed with a cap with an oil filler neck.
The camshaft and coolant pump are driven by a toothed belt from a toothed pulley mounted on the engine crankshaft. The tension of the belt and the direction of its movement along the pulleys is carried out by a tension roller.
The cylinder block is cast iron, with cylinders machined in it. The internal cavities of the block for the coolant are formed during its casting, and the oil supply channels are made by drilling. At the bottom of the cylinder block are five crankshaft main bearings. The main bearing caps are not interchangeable and are marked with the bearing serial number starting from the crankshaft pulley. In the cover of the second main bearing, two threaded holes are made for the oil intake mounting bolts. Steel-aluminum liners of main bearings are installed in the supports and covers. On both sides of the third main bearing support, sockets are made for installing thrust half rings that prevent axial movement of the crankshaft. The front semi-ring is steel-aluminum, the rear is ceramic-metal, yellow on both sides.
Pistons are cast from aluminum alloy. Each piston has two compression rings and one oil scraper ring. Lower compression ring of scraper type with a groove and a sharp edge on the lower plane. A spring expander is installed inside the oil scraper ring.
Fingers - floating type (fixed in the pistons with two spring retaining rings) or fixed in the upper head of the connecting rod by the method «hot fit».
A steel-bronze bushing is pressed into the upper head of the connecting rod. The connecting rod caps are not interchangeable and only fit in one position on the connecting rod.
From below, the crankcase is attached to the cylinder block.
Combined engine lubrication system - under pressure with spraying. The oil pump is an internal gear type driven by the front end of the crankshaft. Through the oil intake, the pump takes oil from the oil pan and pumps it under pressure into the channels of the engine lubrication system. To control the amount of oil in the sump, a measuring probe is installed - a level indicator. Oil filter - full-flow, with a paper filter element and a check valve that prevents oil from flowing out of the lubrication system channels into the oil pan after the engine is stopped.
Oil jets are installed in the main bearings. Oil from the nozzles is supplied to the internal surfaces of the pistons to cool them. Part of the oil enters the upper heads of the connecting rods and flows through the conical holes made in them onto the piston pins, lubricating them.
Channels are drilled in the body of the crankshaft. Oil flows through them to the connecting rod journals, lubricating them. Oil enters the crankshaft channels from the cylinder block through holes in the main bearing shells from the main journals. Technological openings of the channels are closed with stamped steel plugs.
On the left side of the block there is a cavity for installing a coolant pump with a boss for installing an oil filter.
The generator is driven by a V-ribbed belt from the engine crankshaft pulley.
The intake pipe receiver is made of plastic. The exhaust manifold is steel, combined with a catalytic converter. Its connection with the head is sealed with a two-layer metal gasket.
Engines 11186 and 21116 differ from model 11183 in a lightweight connecting rod and piston group.
Pistons with a short skirt.
All piston rings are thinner than previous engines to reduce internal engine friction losses.
Connecting rods - «stab» *.
* The connecting rod and its cover are first made as a single (one-piece) detail. After making holes in the upper and lower connecting rod heads, using a special method «split» lower head. This technology allows you to get the perfect connection between the cap and the connecting rod.