Comment. To compensate for the thermal expansion of the valve stem between the camshaft cam and the valve lifter, a gap is required). For intake valves, the clearance should be 0.15-0.25 mm, and for exhaust valves - 0.30-0.40 mm. The gap is set by selecting the thickness of the shims. The washers are installed in a niche located on the pushers from above. To make it easier to remove the washers, grooves are made on the upper edges of the pushers. The size of the washer is marked on its non-working surface.
![]() | ![]() |
Advice. It is more convenient to divide the work into two stages. First measure the gaps and calculate the thickness of the new washers, and only then purchase and install new washers.
To complete the work you will need:
- a set of flat probes;
- tweezers;
- micrometer (with a measurement limit of 0-25 mm);
- gap adjuster.
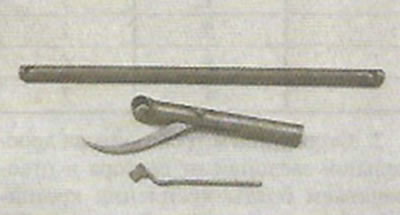
Warning! Checking and adjusting clearances is performed only on a cold engine (at a temperature of about +20°С).
Execution sequence
1. We prepare the car for work («Preparing the car for maintenance and repair»).
2. Remove the cylinder head cover («Cylinder head cover gasket - replacement»).
3. Remove the front timing belt cover («Timing Belt - Checking Condition»).
4. With a medical syringe or a rubber bulb, remove the remaining oil around the valve lifters.
5. We install the valve adjuster on the cylinder head studs and fix it with the nuts that fastened the cylinder head cover.
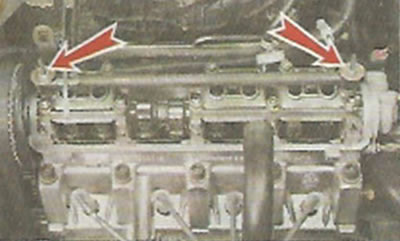
Recommendation. There are several ways to adjust clearances. They differ in the order in which valve clearances are measured. In any case, the clearances are only checked with the valves closed (their pushers are not preloaded by the camshaft cams). If it is difficult to determine the position of the valves, the following method should be followed.
6. Rotating the crankshaft clockwise, set the piston of the first cylinder to the TDC position of the compression stroke.
Comment. The crankshaft can be rotated with a 17 mm ring wrench for its pulley bolt or with a large slotted screwdriver for the flywheel teeth. To do this, remove the bottom cover of the clutch housing («Gearbox - removal and installation»).
7. Turn the shaft from the TDC position to an angle of 40-50° (3 teeth camshaft pulley), with probes of appropriate thicknesses, we determine the gaps in the actuator 1 and 3 of the valves (when counting in order from the camshaft pulley).
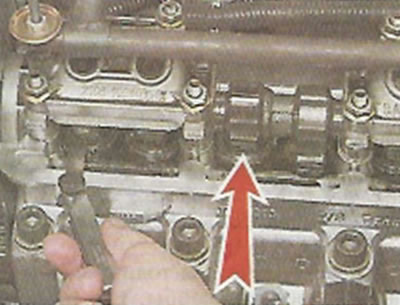
Comment. The gauge should be slightly pinched in the gap between the camshaft cam and the tappet shim.
8. If the gap does not correspond to the norm, turn the pusher with the groove towards you. With the device we drown the valve, holding the pusher from rotation with a screwdriver inserted into the groove. With the fixture lock, we stop the pusher in the lower position.
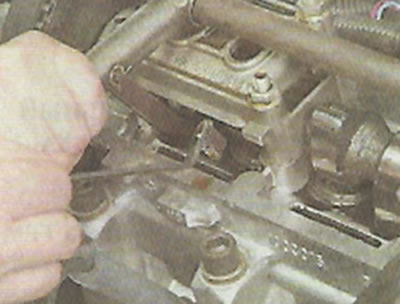
9. Remove the shim with tweezers.
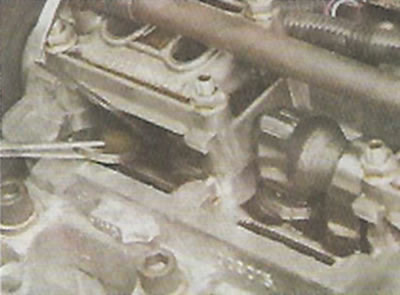
10. By marking on the washer, we determine its thickness. If the inscription is erased, measure the thickness of the washer with a micrometer.
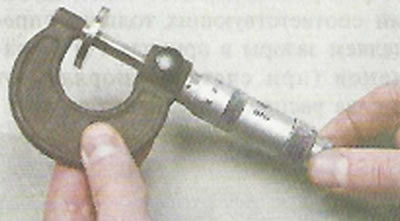
11. We calculate the gap of the new shim using the formula:
- A) for intake valves: Z = Y + X - 0.2 mm;
- b) for exhaust valves: Z = Y + X - 0.3 mm;
where Z is the calculated thickness of the new shim, Y is the thickness of the removed shim; X is the gap determined by the probe.
12. We select a new washer, in which the thickness is close to the calculated (±0.05 mm).
13. Install a new washer in the pusher (marking down).
14. We press the pusher with a fixture and remove the retainer.
15. Observing the sequence indicated in the table. 8.1.3, we check and adjust the clearances in the drive of other valves.
The angle of rotation of the crankshaft from the TDC position of the compression stroke of the first cylinder, deg. | Cam | |||
high school graduation | inlet | |||
40-50 | 1 | 3 | ||
220-30 | 5 | 2 | ||
400-410 | 8 | 6 | ||
580-590 | 4 | 7 |
16. Having removed the device for adjusting the valves, install the removed parts in the reverse order of disassembly.