For disassembly, repair and assembly of the cylinder head on a car, you will need: the same tools as when replacing the head gasket (see «Replacing the cylinder head gasket»), when replacing valve stem seals (see «Replacement of valve stem seals»), as well as the keys «at 13», «at 21».
1. Remove the cylinder head (see «Replacing the cylinder head gasket»).
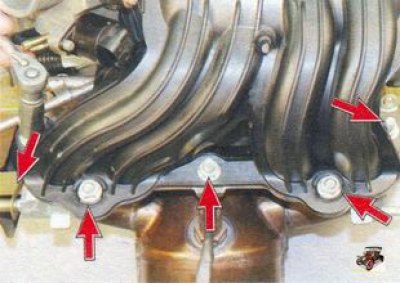
2. Unscrew the five nuts securing the intake module to the intake pipe, and remove the module together with the throttle assembly from the intake pipe studs.
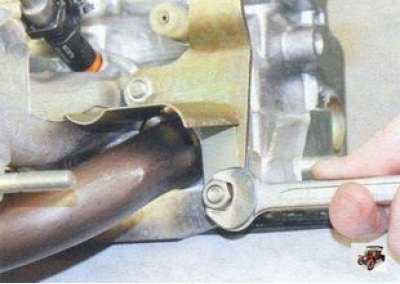
3. Turn away two nuts of fastening of a forward heat-insulating shield and a transport eye, remove a shield and an eye.

4. Turn away two nuts of back fastening of an inlet pipe and the catalyst (the rear heat shield is attached with the same nuts) and remove the rear heat shield. Remove the washers under the shield.
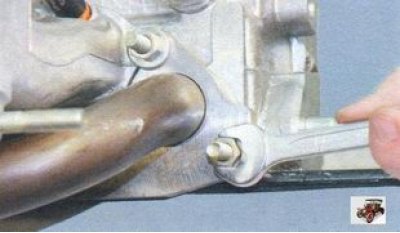
5. Turn away two nuts of forward fastening of an inlet pipe and the catalyst and remove the washers established under them.
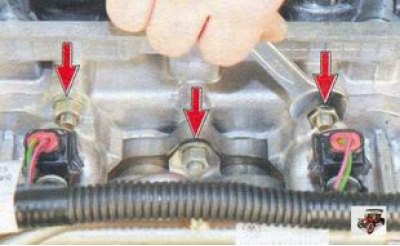
6. Turn off three top nuts of fastening of an inlet pipe and the catalyst...
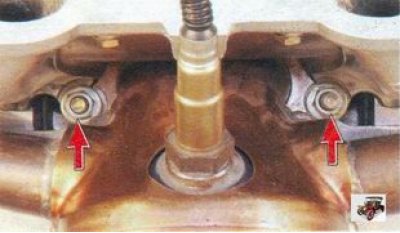
7.... two lower nuts, remove the washers installed under the nuts.
8. Disconnect from a head of the block of cylinders an inlet pipe and the catalyst.
9. Remove the inlet pipe and catalyst gasket from the cylinder head studs.
10. Turn out from a head of the block of cylinders the gauge of the index of temperature of a cooling liquid...
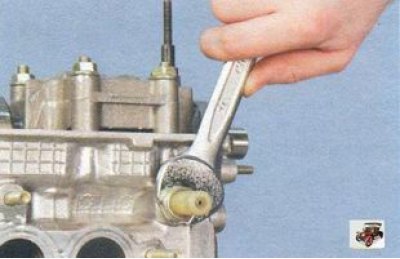
11.... and a warning light sensor for an emergency drop in oil pressure.
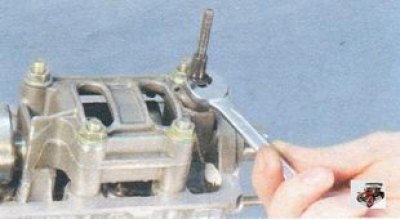
12. To replace the stud securing the cylinder head cover if its thread is damaged, loosen the stud and unscrew it from the cylinder head.
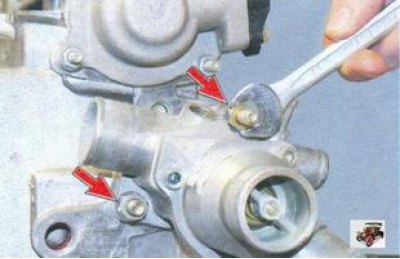
13. Turn away two nuts of fastening of the thermostat, remove the washers established under nuts...
14. Remove the thermostat and the cardboard sealing gasket installed under its nest. Strongly compressed or torn gasket when assembling the cylinder head, replace.
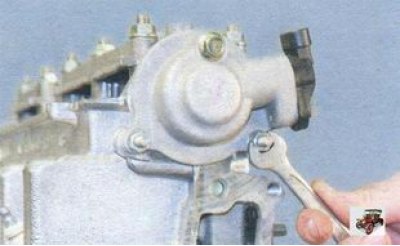
15. Turn away two nuts, turn out a bolt of fastening of a back cover of a head of the block of cylinders and remove a back cover.
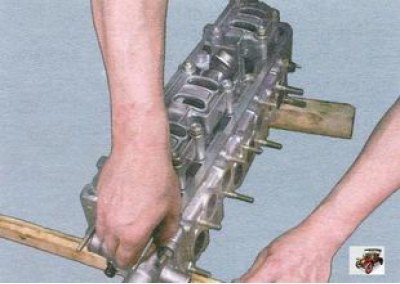
16. Establish a head of the block of cylinders by cases of bearings up, having placed under it wooden linings not to damage valves.
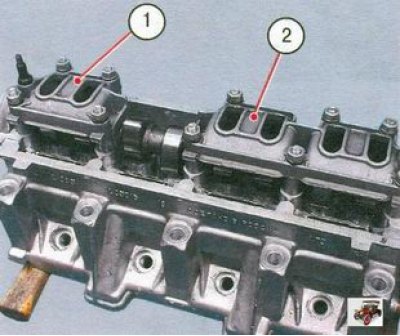
17. Turn away evenly four nuts of fastening of forward 1 and six nuts of fastening of back 2 cases of bearings of a camshaft and remove washers. Then remove both housings.
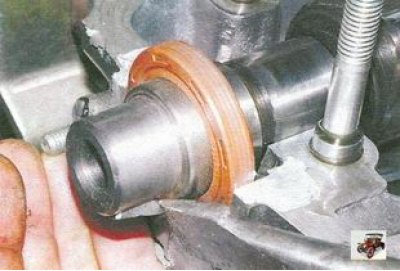
18. If the key in the groove of the camshaft is loose, remove it so as not to lose it.
19. Remove the camshaft from the cylinder head.
20. Remove the oil seal from the camshaft.
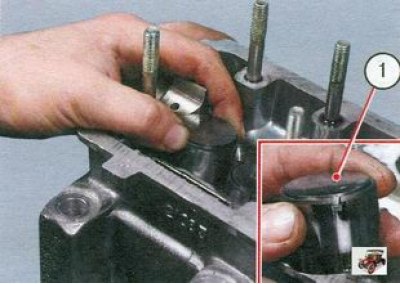
21. Take out pushers of valves together with adjusting washers 1.
22. Clean the combustion chambers from carbon deposits. Inspect the cylinder head. If it has cracks or traces of burnout in the combustion chambers, replace the head. Remove burrs and nicks on the plane of the cylinder head.
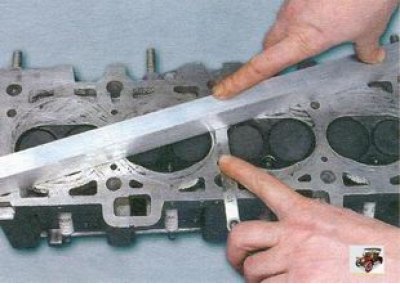
23. Check up flatness of the surface adjoining to the block of cylinders. To do this, place the ruler with an edge on the surface of the head, first in the middle along, and then diagonally, and measure the gap between the plane of the head and the ruler with a feeler gauge. Replace the cylinder head if the clearance exceeds 0.1 mm.
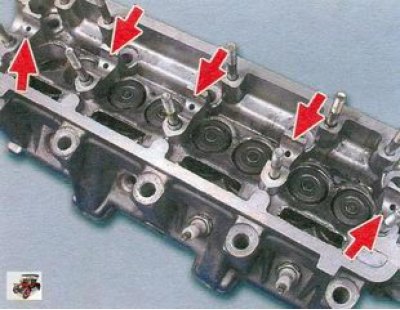
24. Check up a condition of basic surfaces under necks of a cam-shaft on a head of the block of cylinders and cases of bearings. If at least one of them has signs of wear, scoring or deep scratches, replace the cylinder head and bearing housings.
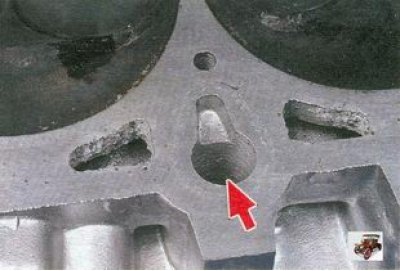
25. Flush the oil passages. To do this, plug the vertical oil passage on the side of the combustion chamber (the channel is located between the 3rd and 4th cylinders)...
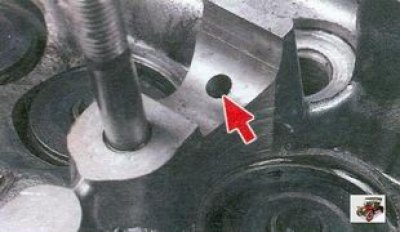
26.... pour gasoline into the oil channels in all camshaft bearings and hold for 15-20 minutes. Pour out the gasoline, remove the plug and finally flush the oil passages with gasoline using a blower.
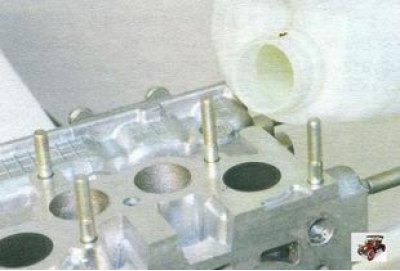
27. To check the tightness of the valves, pour kerosene into the inlet and outlet channels of the cylinder head. If within 3 minutes kerosene does not leak from the channels into the combustion chambers, the valves are tight. Otherwise, rub (see «Lapping of valves») or replace valves.
28. Install a suitable stop, such as a bearing, under the valve to be removed.
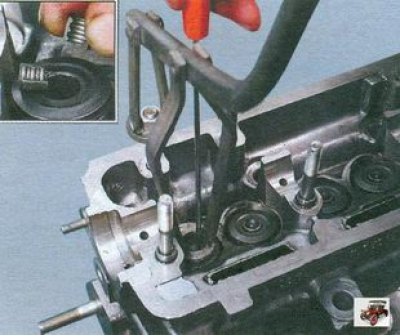
29. Install the valve spring compressor and compress the valve springs with it. Remove two crackers with a screwdriver or tweezers.

30. Remove the upper spring plate, outer and inner valve springs. Similarly, remove crackers, plates and springs of the remaining valves.
31. Mark the valves with cylinder numbers, for example, mark them.
32. Pushing the valves from below, remove them from the block head.
33. Remove valve stem seals with tool or pliers (see «Replacement of valve stem seals»).
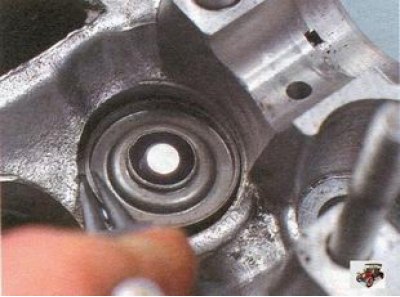
34. Remove the lower plates of the valve springs.
35. Clean valve deposits with a suitable tool (e.g. with a metal brush). Then carefully inspect the valves.
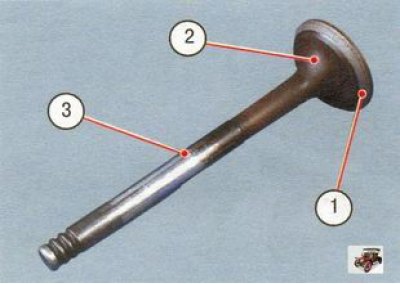
36. Replace valves with the following defects: deep marks and scratches on the working chamfer 1, cracks, deformation of the rod 3, warping of the plate 2, traces of burnout. Shallow risks and scratches on the working chamfer can be removed by lapping the valves (see «Lapping of valves»).
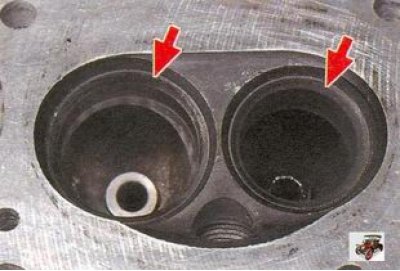
37. Check the condition of the valve seats. Valve seat faces must be free of wear, pitting, corrosion, etc. The valve seats can be replaced by a specialist workshop. Minor damage (minor scratches, scratches, etc.) can be removed by lapping valves (see «Lapping of valves»).
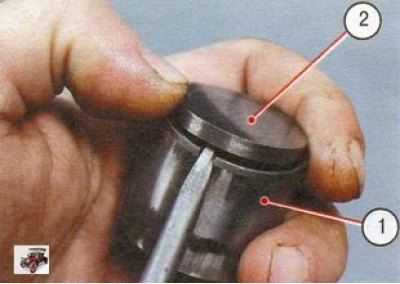
38. Inspect the valve lifters. If there are scuffs, scratches and other defects on the working surface of 1 pusher, replace the valve lifters. Measure the outer diameters of the valve lifters (see «Valve lifter replacement»), replace worn valve lifters. On the working surfaces of the adjusting washers 2 there should be no burrs, nicks, scratches, traces of stepped or uneven wear, metal rubbing. Washers with such defects must be replaced. Concentric burn-in marks with camshaft cams are allowed on the washers.
Clearances between the valve and the guide sleeve, mm:
- nominal for inlet valves - 0.022-0.055
- nominal for exhaust valves - 0.029-0.062
- maximum allowable for intake and exhaust valves - 0.300
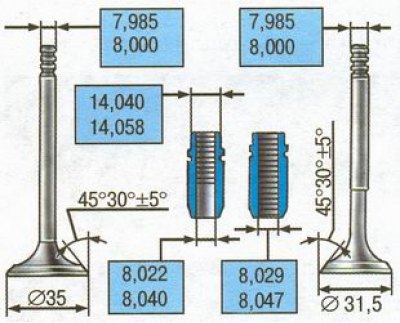
Pic. 4.5. Dimensions of valves and valve guides
39. Check up backlashes between directing plugs and valves. The clearance is calculated as the difference between the diameters of the hole in the sleeve and the valve stem (pic. 4.5). Checking the clearance is recommended to be carried out by a specialized car workshop, since a special tool is needed to measure the diameter of the valve guides (caliper).
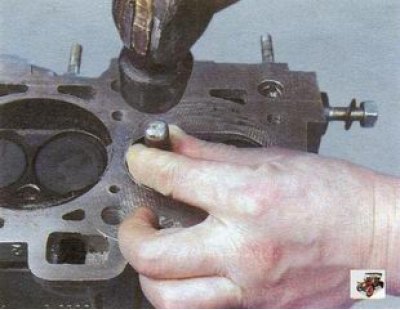
40. If the gap does not reach the maximum allowable, you can try to eliminate it by replacing the valve. If this fails or the clearance exceeds the limit, replace the valve guide. To do this, press out the defective valve sleeve from the side of the combustion chamber with a special mandrel.
41. After lubricating the valve guide with engine oil, insert it into a special mandrel and press it from the side of the camshaft until the retaining ring stops in the cylinder head. Ream the hole in the sleeve using a reamer to 8.022-8.040 mm for intake valves and to 8.029-8.047 mm for exhaust valves.
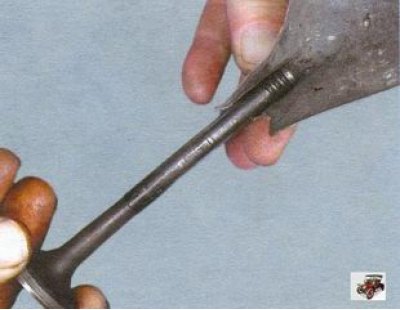
42. If an old valve is being installed, deburr the cracker grooves. After that, it is necessary to grind the valve to the seat (see «Lapping of valves»).
43. Install the valves in the cylinder head in accordance with the previously marked markings, after lubricating the rods with engine oil.
44. Install the lower plates of the valve springs.
45. Install valve stem seals (see «Replacement of valve stem seals»).
46. Install the camshaft and bearing housings (see «Replacement of valve stem seals»).
47. Install on the head of the block all the parts and assemblies removed during its disassembly.
48. After installing the block head on the engine, check the clearances in the valve drive and, if necessary, adjust them (see «Valve clearance adjustment»).