To complete the work you will need:
- three- or two-jaw puller;
- homemade mandrel from the cup puller kit.
Disassembly
1. Remove the generator from the car (see above, «Generator - removal and installation»).
2. Remove the voltage regulator (see «Voltage regulator - replacement»).
3. Prying with a screwdriver, remove the ends of the stator winding leads from the spring-loaded contacts of the rectifier unit.
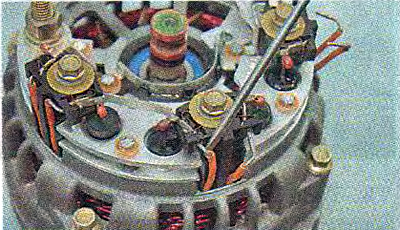
Comment. You can check the condition of the rectifier unit and the stator windings without disassembling the generator further. It is enough to carefully bend the winding leads to the sides. The verification procedure is the same as shown below.
4. Using an 8 mm spanner, unscrew the three bolts securing the rectifier unit (remembering how the insulating and thrust washers are installed).
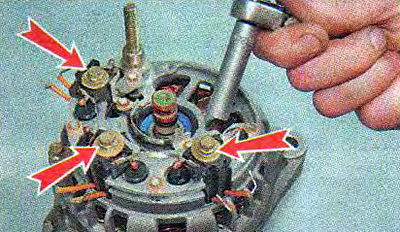
5. Using a 12 mm wrench, unscrew the nut of the contact bolt.
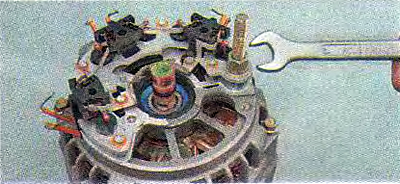
6. Remove the rectifier block.
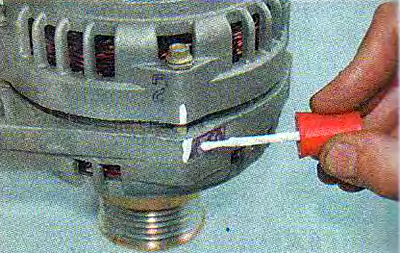
7. Mark with a marker the relative position of the front and rear covers of the generator (to simplify assembly).
8. Using an 8 mm socket wrench, unscrew the four bolts that tighten the front and rear covers of the generator.
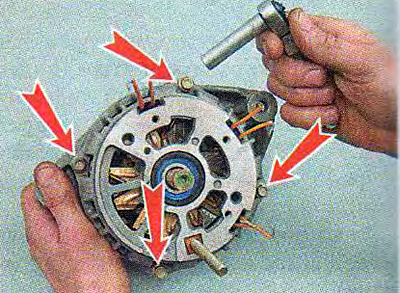
9. With a slotted screwdriver, carefully push the covers of the generator apart.
10. Remove the back cover, remove the contact bolt from it (with an insulating washer) and a plastic bearing bush.
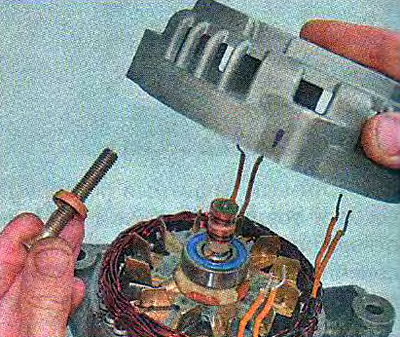
Recommendation. To determine the technical condition of the rear bearing, shake from side to side and vigorously rotate its outer ring. The bearing should not have significant play, the ring should rotate freely without jamming and extraneous noise. A defective bearing must be replaced.
11. Mark with a marker the relative position of the stator and the rear cover.
12. Prying with a screwdriver, remove the stator from the back cover of the generator.
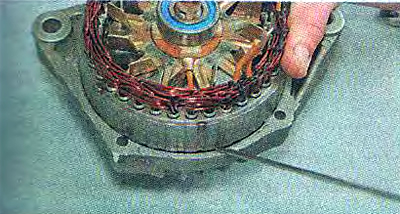
13. To determine the technical condition of the front bearing, holding the pulley with your hand, rotate and shake the front cover from side to side.
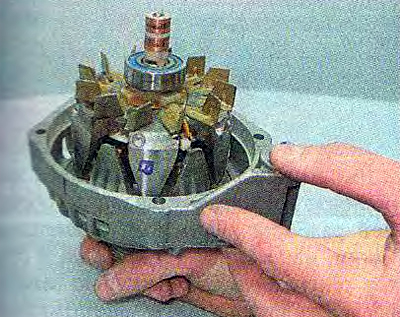
Recommendation. If the bearing seizes, has significant play, or makes a lot of noise when the cover is rotated vigorously, it must be replaced.
Advice. The manufacturer does not recommend changing the front rotor bearing, since the bearing is rolled in the front cover of the generator. But, given that the cost of the bearing is much lower than the cost of a new front cover and, especially, the generator assembly, it is advisable to press out and replace the faulty bearing.
14. If it is necessary to replace the front bearing of the generator with a 24 mm socket wrench, unscrew the pulley fastening nut, holding the pulley with sliding pliers.
15. Remove pulley 3 with spring and flat washers 2, spacer 1 from the rotor shaft.
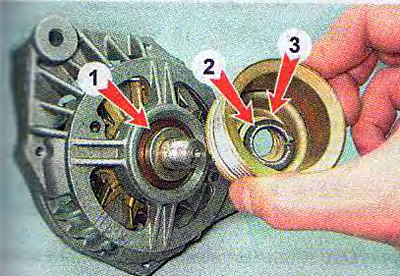
16. By blows of a hammer with a rubber head, we press the rotor out of the front bearing (to do this, we bait the pulley fasteners onto the threads of the rotor shaft flush with the end).
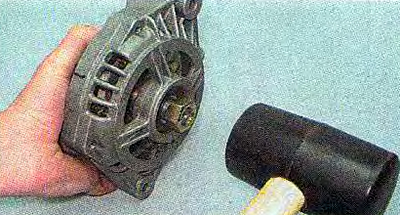
17. If it is necessary to replace the front bearing of the generator, install the front cover in a vise.
18. Having selected suitable mandrels from a set of cup puller, we press the bearing out of the bore of the front cover.
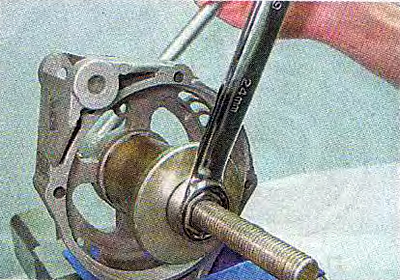
19. Having fixed the rotor in a vice with soft pads on the jaws, using a universal puller of a suitable size, we press the rear bearing from the rotor shaft.
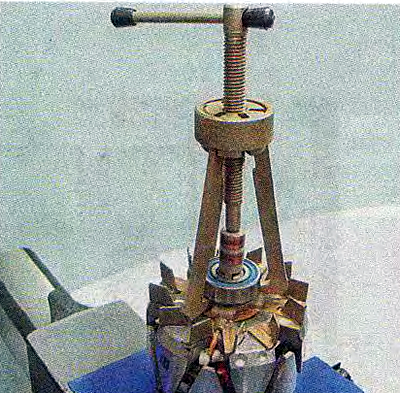
Examination
1. Applying the ohmmeter probes to the slip rings of the rotor, we check the excitation winding for an open circuit. The resistance of a good excitation winding should be 5-10 ohms.
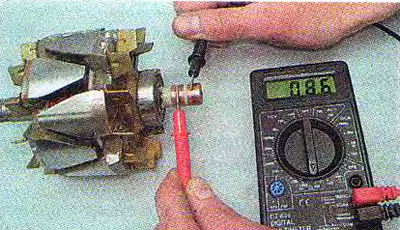
2. By connecting the ohmmeter probes to any slip ring and to the rotor, we check the excitation winding for a short circuit to «mass». With a good rotor winding, the ohmmeter should show an infinitely large resistance.
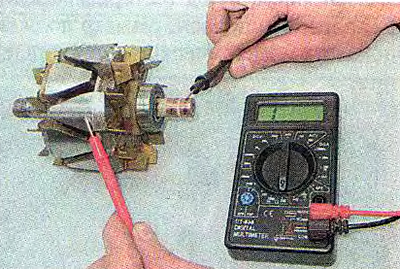
3. Alternately connecting the ohmmeter probes to the terminals of the stator winding, we check the stator windings for an open circuit. In the absence of a break, the ohmmeter will show a small electrical resistance.
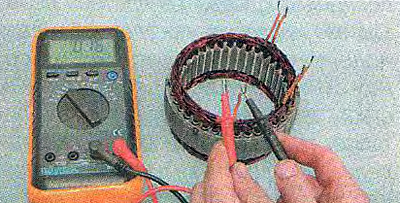
4. By connecting the ohmmeter probes to any winding terminal and to the stator, we check the stator winding for a short circuit to «mass». If there is no short circuit, then the ohmmeter should show infinite resistance.
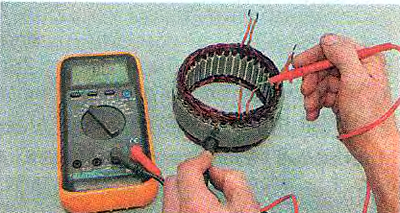
Replace defective rotor and stator.
Comment. A good semiconductor diode conducts electricity in only one direction. If the diode does not conduct current or conducts current in both directions, then it is faulty.
5. We connect the probe of the negative terminal of the ohmmeter to the terminal of the diode, and the probe of the positive terminal to the body of the diode under test (or to the plate into which it is pressed). A good diode should not pass current (resistance tends to infinity).
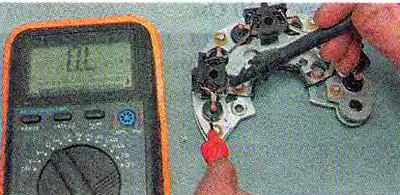
6. We change the probes of the tester in places. If the diode is good, the ohmmeter should show electrical resistance.
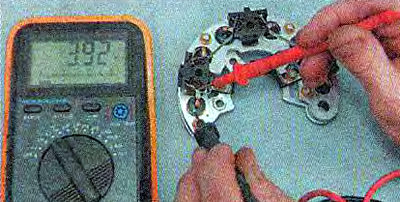
7. Similarly, we check other diodes of the rectifier unit.
Assembly
Warning. Before pressing the bearing into the front cover of the generator, it is necessary to check the seat of the bearing and, if necessary, restore the chamfer with a knife or scraper where the edges of the hole have remained jammed. When pressing the front bearing into the cover, the force must be applied only to the outer ring of the bearing.
1. Having selected suitable mandrels from the cup puller set, we press the new bearing into the front cover of the generator until it stops.
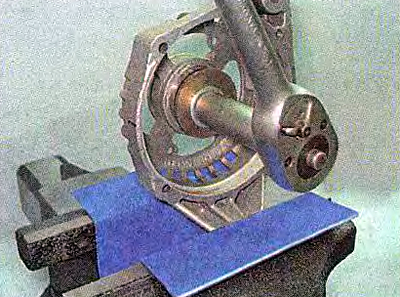
2. Applying light blows with a hammer through a drift, we restore the rolling of the bearing in the cover.
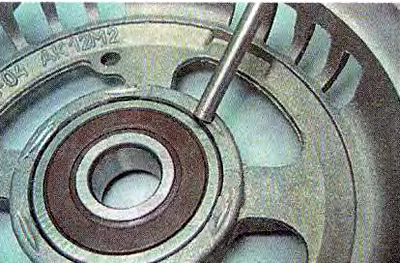
3. Using a tube of suitable diameter (19mm deep socket can be used) until it stops, press the rear bearing onto the rotor shaft.
Warning! Before installing the alternator rear bearing, make sure that the shaft is securely clamped in a vise. Place a wooden block of a suitable size under the rotor shaft so that the front impeller of the rotor is not damaged during pressing. To avoid damage to the bearing, strikes should only be applied to the inner ring of the bearing.
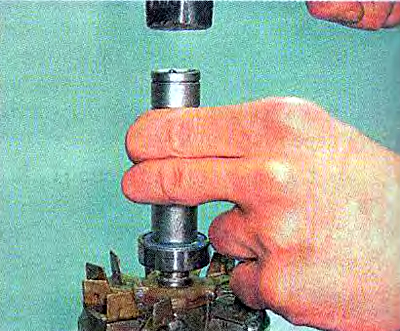
Further assembly of the generator is carried out in the reverse order of disassembly. At the same time, we combine the marks applied to the covers and the generator stator. We finally tighten the coupling bolts evenly, crosswise, in several stages of half a turn. By tightening the bolts, we are convinced of the easy rotation of the rotor (rotor sticking can be caused by misaligned caps). Before installing the plastic casing, we make sure that the stator winding leads are securely fastened.