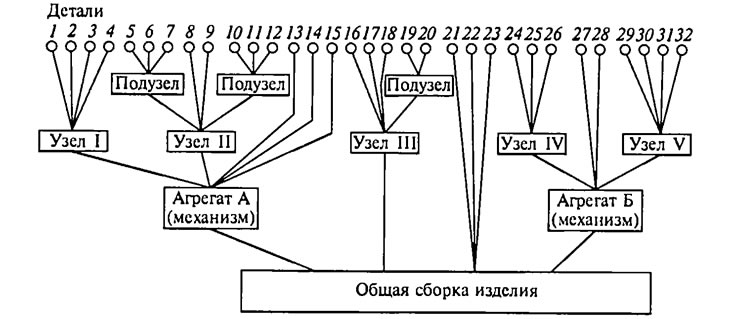
Рис. 4.23. Схема общей сборки автомобиля
Формы сборки
В зависимости от типа производства, трудоемкости процесса сборки и особенностей автомобиля в настоящее время различают две организационные формы сборки: поточную и непоточную.
Поточный метод сборки считается наиболее совершенной формой сборки агрегатов и автомобилей. Его применение целесообразно в организациях по ремонту полнокомплектных автомобилей со значительной производственной программой. Собираемый автомобиль принудительно перемешается по конвейеру. Режим работы конвейера (как правило, периодический) устанавливается в зависимости от производственной программы, такта выпуска, сложности сборочных операций и различных технологических факторов. Промежуток времени между выходом со сборки двух готовых автомобилей или его узлов называется тактом сборки.
Для бесперебойной поточной сборки необходимо своевременное обеспечение линии требующимися деталями и узлами. При этом сборка узлов должна быть согласована с тактом общей сборки агрегата или автомобиля. Сборка на конвейере с периодическим перемещением проводится в периоды его остановки.
Признаки, характеризующие поточную сборку:
- 1) за каждым рабочим местом закреплена определенная операция;
- 2) собранный на предыдущем рабочем месте агрегат или автомобиль передается на следующую операцию немедленно по окончании предыдущей;
- 3) на всех рабочих местах сборочной линии работа синхронизирована и выполняется в соответствии с установленным тактом;
- 4) сборка механизирована.
Сборка грузового автомобиля проводится в такой последовательности. На базовую сборочную единицу (раму) устанавливают собранные агрегаты и узлы: передний и задний мосты, карданную передачу, рулевое управление, двигатель в сборе с коробкой передач, радиатор, кабину, колеса и остальные узлы, механизмы и детали. Необходимые регулировочные работы осуществляют непосредственно в процессе сборки.
Непоточный метод сборки характеризуется выполнением сборочных операций на постоянном рабочем месте, к которому подаются все детали и узлы собираемого автомобиля. При этом сборка может быть выполнена по принципу концентрации и дифференциации операций.
При концентрации сборочных операций автомобиль собирается на одном рабочем (сборочном) месте. Однако при такой организации технологического процесса сборку должны проводить высококвалифицированные сборщики, причем времени на сборку затрачивается больше.
При дифференциации сборочных операций сборка выполняется параллельно на нескольких рабочих местах, что значительно ускоряет этот процесс при некотором снижении качества сборки.
Средства механизации и автоматизации сборочных процессов
Эти средства, устанавливаемые на рабочих местах, обеспечивают значительное повышение производительности и качества труда при сборке, а также снижение трудоемкости и себестоимости продукции. К ним относятся устройства для установки и закрепления изделий и манипуляций ими, специализированная тара для деталей и узлов и механизированные (автоматизированные) механические устройства для выполнения основных сборочных операций.
При осуществлении сборочных операций применяют механизированно-ручной и механизированный инструмент с электрическим, пневматическим и гидравлическим приводом. Наиболее широкое применение находят электрические и пневматические механизированно-ручные инструменты.
Приработка контактных поверхностей и испытание изделия
Приработка — это процесс изменения размеров, макро- и микрогеометрии, а также физико-механических свойств трущихся поверхностей с целью оптимизации их параметров за сравнительно короткий промежуток времени. Приработке (обкатке) и испытанию подвергаются такие агрегаты, как двигатель, коробка передач, редуктор, ведущий мост и др. Эти процессы осуществляются на установках, оснащенных необходимыми приводными и нагрузочными устройствами, комплексом контрольно-измерительных средств и инженерных коммуникаций.
Приработка двигателей осуществляется в три стати и: холодная приработка, горячая без нагрузки и горячая с нагрузкой. На стадии холодной приработки электродвигатель потребляет ток, на стадии горячей приработки электродвигатель работает в генераторном режиме, вырабатывая ток, который направляется в сеть организации В процессе приработки проводятся необходимые регулировки, оценивается техническое состояние двигателя и качество ремонта. В конце процесса приработки двигатель подвергается испытанию на соответствие ТТ.
Приработка и испытание агрегатов трансмиссии (коробка передач, раздаточная коробка, редуктор, ведущий мост и др.) осуществляется на установках, имеющих приводные и нагрузочные устройства, а также контрольно-измерительные средства.
Коробки передач прирабатывают и испытывают на установленных режимах без нагрузки и под нагрузкой на всех передачах, контролируя при этом легкость их переключения, отсутствие самовыключения, уровень шума, степень нагрева контролируемых участков и т.д.
Редукторы и задние мосты прирабатывают и испытывают при различной частоте вращения ведущей шестерни без нагрузки и с нагрузкой до полного торможения поочередно одного из барабанов. При этом одновременно контролируют уровень и характер шума шестерен редуктора, герметичность соединений, степень нагрева подшипниковых узлов и т.п. При наличии повышенного шума шестерен редуктора производится дополнительная регулировка по контакту и боковому зазору в зубьях.
Выпуск автомобиля из ремонта
Собранный автомобиль должен быть смазан, а агрегаты заправлены маслами в соответствии с ТТ. Все регулируемые механизмы и узлы должны быть отрегулированы с соблюдением ТТ. После этого автомобиль поступает на пост контроля и испытания.
В процессе контроля и испытания проверяется комплектность автомобиля, качество сборки, исправность функционирования и правильность регулировки отдельных механизмов и приборов в соответствии с ТТ.
Испытания автомобиля проводят на стендах с беговыми барабанами, где проверяется работа двигателя, агрегатов трансмиссии и ходовой части. При этом оцениваются основные эксплуатационно-технические качества автомобиля, включая мощность двигателя, тяговое усилие па ведущих колесах, расход топлива при различных скоростных и нагрузочных режимах, путь и время разгона до заданной скорости, потерю мощности на трение в агрегатах и ходовой части, наибольший допустимый тормозной! путь при определенной скорости, интенсивность действия тормозных механизмов. При этом проверяется и при необходимости регулируется установка углов управляемых колес и т.п.
После стендовых испытаний каждый автомобиль проходит испытание пробегом, например на расстояние 40 км с грузом, равным 75% грузоподъемности автомобиля, со скоростью нс более 40 км/ч по дорогам с твердым покрытием. При пробеге проверяют исправность и надежность работы всех систем, механизмов и соединений. После испытания пробегом автомобиль тщательно осматривают, после чего все выявленные дефекты устраняют.
Затем автомобиль поступает на окончательную окраску и на склад готовой продукции. На каждый выпускаемый из ремонта автомобиль АРО выдает заказчику паспорт, в котором фиксируется комплектность, техническое состояние и соответствие отремонтированного автомобиля техническим требованиям на его КР. ТТ устанавливают гарантированную исправную работу автомобиля в течение определенного времени и определенного пробега за этот период. На протяжении гарантийного срока все обнаруженные заказчиком неисправности по вине АРО должны быть устранены в течение трех суток со дня предъявления рекламации.
В настоящее время гарантийный срок эксплуатации автомобилей составляет 12 мес со дня выдачи из ремонта при пробегах:
- не более 20 тыс. км — для автобусов;
- не более 16 тыс. км — для прочих автомобилей.
При выпуске автомобиля из КР прилагаются следующие документы:
- к автомобилю:
- 1) паспорт с отметкой АРО о проведенном ремонте с указанием даты выпуска из ремонта;
- 2) новые номера шасси и двигателя;
- 3) основной цвет окраски автомобиля;
- 4) инструкция по эксплуатации с указанием особенностей эксплуатации отремонтированного автомобиля в обкаточный и гарантийный периоды;
- к двигателю:
- 1) паспорт;
- 2) инструкция но эксплуатации с указанием особенностей установки и эксплуатации двигателя в обкаточный и гарантийный периоды.
Выпуск из КР автомобилей, их составных частей и деталей (комплектов деталей) оформляется соответствующим приемо-сдаточным актом.