Технологический процесс сборки включает в себя ряд последовательных операций по установу и созданию различных видов соединений составных частей изделия, в том числе операций контроля, регулировки и испытания.
Процессу сборки изделия предшествует этап комплектования, который позволяет сгруппировать различные по качеству детали: восстановленные на АРО, годные (без ремонта, с допустимыми износами) и запасные части. Безусловно, параметры всех этих деталей имеют те или иные отклонения от заданных в рабочих чертежах, но они допускаются к дальнейшей сборке. В целях обеспечения номинальных значений посадок в соединениях рекомендуется в большей степени применять метод групповой сборки.
Контроль и сортировку легких и транспортабельных деталей рекомендуется организовывать в комплектовочном отделении на специализированных постах, крупногабаритных деталей и узлов — на постах контроля при их восстановлении. Для повышения производительности труда и эффективности комплектовочных работ необходимо использовать краны-штабелеры. При этом доставку сборочных комплектов к постам сборки целесообразно осуществлять с помощью подвесных грузонесущих толкающих конвейеров. В условиях крупных АРО эти операции необходимо выполнять с помощью устройств, обеспечивающих адресование грузов.
Технологический процесс сборки
Этот процесс разрабатывается поэтапно на основе ЕСТПП, ЕСТД и других стандартов в такой последовательности:
- 1) проводится технологический анализ сборочных чертежей, уточнение разбивки изделия на сборочные единицы, оценка уровня технологичности и ремонтопригодности изделия и его частей, а также разработка рекомендаций по их улучшению;
- 2) анализируются плановые задания и организационные формы сборочного процесса;
- 3) осуществляется размерный анализ основных соединений и выбор методов сборки и их сочетаний для изделия в целом;
- 4) уточняются ТТ на сборку соединений, узловую и общую сборку изделий, контроль, регулировку и испытание сборочных единиц и изделия в целом;
- 5) разрабатывается технологическая схема сборки для узла и изделия. В качестве примера подобная схема сборки ступицы шкива приведена на рис. 4.20;
- 6) оптимизируется состав, содержание и последовательность операций и переходов;
- 7) нормируется технологический процесс;
- 8) выбирается стандартное оборудование и оснастка и одновременно заказываются нестандартизованные средства технологического оснащения, включая средства контроля, испытаний и транспортирования;
- 9) проектируется поточная линия с обеспечением синхронизации сборочных операций и разработкой планировки и организации линии (участка, цеха);
- 10) выявляются требования техники безопасности, производственной санитарии и охраны окружающей среды;
- 11) проводится технико-экономический анализ и обоснование принятого варианта технологического процесса сборки изделия;
- 12) оформляется технологическая документация.
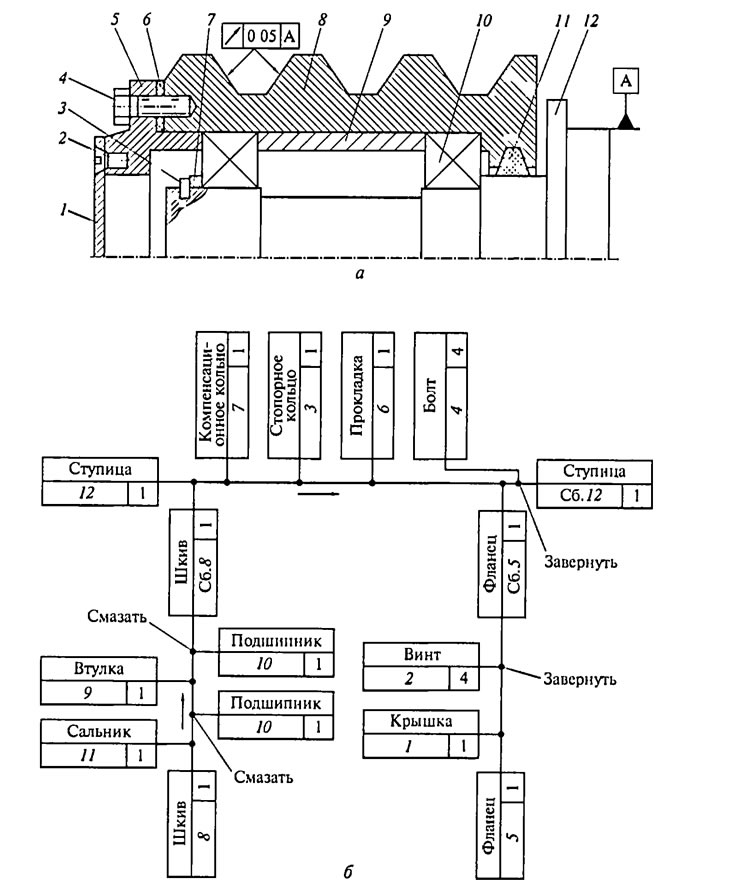
Рис. 4.20. Сборка ступицы шкива: а - конструкция ступицы шкива: 1 - крышка; 2 - винт; 3 - стопорное кольцо; 4 - болт; 5 - фланец; 6 - прокладка; 7 - компенсационное кольцо; 8 - шкив; 9 - втулка; 10 - подшипник; 11 - сальник; 12 - ступица; б - технологическая схема сборки ступицы (в рамках пол названиями деталей левая цифра обозначает номер позиции детали, а правая - число таких деталей)
Для сокращения затрат труда и времени при проектировании технологических процессов сборки целесообразно применение ЭВМ.
Механизация и автоматизация сборочных работ
Повышение производительности и качества труда при сборке изделий, снижение трудоемкости и себестоимости продукции зависят от уровня механизации и автоматизации сборочных работ. В передовых АРО в настоящее время доля механизации и автоматизации составляет 20...25%, что следует считать недостаточно высоким уровнем. Поэтому одним из главных направлений в улучшении процесса сборки является комплексная механизация и автоматизация основных и вспомогательных операций.
Для выполнения сборочных операций в АРО применяют механизированно-ручной и механизированный инструмент с электрическим, пневматическим и гидравлическим приводами.
Примеры сборочных работ по сборке узлов, агрегатов и машин
Сборочные работы представляют собой ряд последовательных операций, качество которых определяется:
- тщательностью очистки, промывки и обдувки сжатым воздухом деталей, поступающих на сборку;
- соответствием геометрических параметров, шероховатости поверхности, неуравновешенности деталей и узлов параметрам, заданным ТТ
- отсутствием разукомплектования сопряженных деталей; качеством выполнения комплектовочных работ;
- применением при сборке соответствующего оборудования, приспособлений и инструментов, обеспечивающих заданное качество сборки соединений;
- соблюдением регламентированных технологических режимов, инструкций и требований к сборке соединений;
- использованием при сборке рекомендуемых материалов, уплотнительных и стопорных элементов и др.
Доля резьбовых соединений в конструкции автомобиля достигает 75% всех соединений, при этом трудоемкость их сборки составляет около 40% обшей трудоемкости сборочных работ. Процесс сборки резьбовых соединений состоит из следующих этапов:
- 1) подача и установка сопрягаемых деталей в исходное положение;
- 2) ввертывание (навинчивание) и затяжка одной из деталей;
- 3) дотяжка динамометрическим ключом до заданного для этого соединения крутящего момента;
- 4) стопорение (при необходимости) и контроль соединения.
Максимальное усилие затяжки устанавливается из условия прочности болта (шпильки, винта), минимальное — из условия нераскрытая стыка. Для метрических резьб (с углом профиля 60°) крутящий момент на ключе Мкр, Н·м, пропорциональный силе затяжки, может быть рассчитан по формуле [3]

где Р — осевая сила; Q — сила трения; dcp — средний диаметр резьбы; D и dо — соответственно наружный и внутренний диаметры опорных кольцевых поверхностей гайки (головки болта); fр и fт — коэффициенты трения соответственно в резьбе и на торце опорной поверхности гайки.
Установлено, что обрыв шпилек и болтов происходит в основном из-за перекоса торца гайки (головки болта) и несоосности болтов, шпилек и винтов относительно осей резьбовых отверстий. Единственный способ предотвращения этих явлений — правильная подготовка базовых поверхностей.
Сборка соединений с натягом осуществляется под действием осевой силы или температурного воздействия путем нагрева охватывающей или охлаждения охватываемой детали. Основными условиями нормальной сборки с натягом являются обязательное применение приспособлений, обеспечивающих соосность сопрягаемых деталей в момент сборки, и наличие заходных фасок в зоне начала контакта у обеих сопрягаемых деталей.
Осевая сила при запрессовке Р зависит от следующих показателей: натяга, геометрических параметров сопряжения, физикомеханических свойств материалов сопрягаемых деталей, шероховатости поверхности, наличия смазки и др.
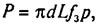
где d и L — соответственно номинальный диаметр и длина сопряжения; fз — коэффициент трения при запрессовке; р — давление на поверхность пресса (определяется по формуле [3], в которую входят перечисленные показатели).
Сборка с термовоздействием повышает прочность соединений в 1,5—2,5 раза по сравнению с механической запрессовкой.
Зубчатые передачи — наиболее распространенные виды передач в автомобиле, в значительной степени влияющие на его безотказность и долговечность, Работоспособность зубчатых передач зависит от геометрической точности зубчатых колес и зацепления (боковой зазор, форма, площадь и положение пятна контакта зубьев).
Сборка зубчатых передач осуществляется методом полной взаимозаменяемости, поэтому все поступающие на сборку зубчатые колеса и корпусные детали должны строго соответствовать ТТ, приведенным в чертеже. Для контроля параметров зубчатых колес применяются зубомеры, шагомеры, толщиномеры, а также различные приборы и приспособления, позволяющие установить межосевое расстояние, плавность работы, контакт зубьев и т.п,
Точность сборки конических и гипоидных зубчатых передач обеспечивается регулированием посредством компенсаторов — набора регулировочных шайб, колец и прокладок. Для повышения производительности и качества сборки конических и гипоидных передач применяют контрольно-обкаточные стенды.
Балансировка деталей и узлов снижает их дисбаланс и в значительной степени повышает долговечность и надежность быстровращающихся деталей и узлов, а следовательно, и машин в эксплуатации. Поэтому в технологии изготовления и ремонта деталей автомобиля обязательно предусматривается балансировка таких деталей, как коленчатые и карданные валы, маховики, шкивы, колеса, диски сцепления и т.п.
Причинами возникновения дисбаланса деталей являются:
- неточность размеров и ТТ на пределы допуска;
- наличие необработанных поверхностей;
- неравномерная плотность металл а детали;
- неравномерное нанесение металла в процессе восстановления детали;
- погрешности сборки.
Таким образом, дисбаланс возникает при изготовлении и восстановлении деталей, а также при сборке узлов и агрегатов В процессе эксплуатации и ремонта машины он, как правило, повышается.
Для устранения дисбаланса применяют два вида балансировки: статическую и динамическую. При этом основная цель балансировки — выявить величину смещения центра масс детали от оси ее вращения и определить место и величину груза (или объема металла, подлежащего удалению), исключающего дисбаланс до величины, заданной ТТ.
Статическая балансировка применяется для деталей относительно большого диаметра и малой ширины или толщины (L < D) и проводится на призмах или роликах, установленных на подшипники. При свободном прокручивании деталь останавливается в положении, при котором «тяжелое место» находится в ее нижней части. После этого подбирается и закрепляется в верхней точке детали такой грузик или кусок пластилина, который уравновешивает имеющееся «тяжелое место». В этом случае деталь останавливается в произвольном положении при ее повторном вращении. Далее определяют массу грузика (пластилина) и в этом месте приваривают соответствующий груз или с противоположной стороны удаляют (например, высверливанием) часть детали такой же массы.
Для статической балансировки рекомендуется известное устройство, приведенное на рис. 4.21. Порядок балансировки заключается в следующем: рейка 2 (без детали 6, но с динамометром 7). находящаяся на подшипниковой опоре 10, уравновешивается при помощи груза 1, что фиксируется индикаторной головкой 3. После этого на ось 5 устанавливают деталь (желательно сориентировать ее по шпоночному пазу) и динамометром, прилагая усилие P1, приводят рейку в горизонтальное положение в соответствии с показаниями индикаторной головки. При этом фиксируют усилие Р1.
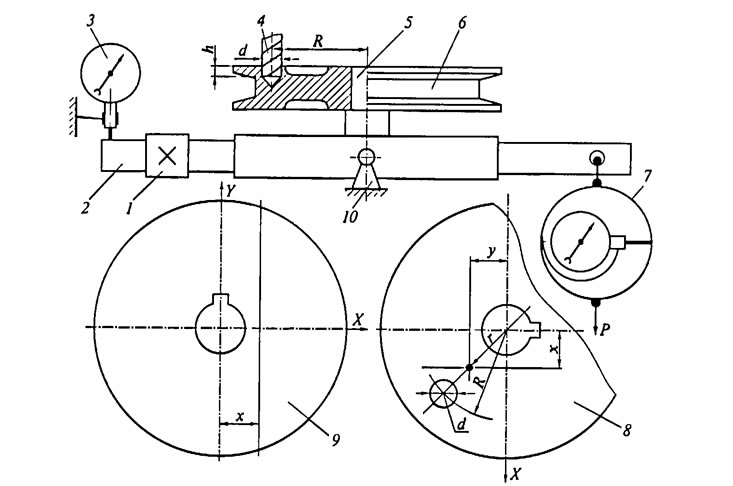
Рис. 4.21. Схема статической балансировки: 1 - уравновешивающий груз; 2 - рейка; 3 - индикаторная головка; 4 - сверло для удаления металла из «тяжелого места»; 5 - ось устройства; 6 - балансируемая деталь (шкив); 7 - динамометр, оснащенный индикаторной головкой; 8 - шкив после второго этапа балансировки; 9 - шкив после первого этапа балансировки; 10 - подшипниковая опора
После этого поворачивают деталь на угол 90° и повторяют те же действия, в результате чего определяется усилие Р2.
Таким образом, получаю г следующие данные: в первом случае — смещение силы тяжести х (справа от оси Y), а во втором — смещение силы тяжести у (слева от оси X). На перекрестье этих направлений, на расстоянии r, и находится центр тяжести детали.
Зная исходный вес детали G, определяют значения х и у (см. рис. 4.21):

Теперь на продолжении вектора r, на выбранном расстоянии высверливается отверстие диаметром d и глубиной h, что обеспечивает балансировку детали.
Динамическая балансировка свойственна деталям и узлам, у которых L >> D (коленчатые и карданные валы, коленчатый вал в сборе с маховиком и сцеплением и т.п.). Она характеризуется наличием двух результирующих неуравновешенных масс, расположенных в двух (обычно крайних) плоскостях коррекции, а также моментом дисбаланса относительно центра масс. Дисбаланс определяют для каждого конца детали, при этом за единицу измерения принимают г·см.
Процесс динамической балансировки осуществляется на специальном балансировочном станке, принципиальная схема которого приведена на рис. 4.22. Сущность динамической балансировки заключается в следующем: деталь (коленчатый вал) (У устанавливают на упругие опоры 7 и 9 и приводят во вращение (с требуемой скоростью) от привода 1 через эластичную соединительную муфту 6, предварительно закрепив опору 9. Тогда опора 7, имеющая возможность изгибаться под действием динамических нагрузок (дисбаланса), будет отклоняться от своего номинального положения на некоторую величину. Значение этой величины фиксируется с помощью индукционного датчика 11, вибрирующего вместе с деталью относительно неподвижного постоянного магнита 12. Учитывая предварительную тарировку опоры 7, можно определить величину дисбаланса по амплитуде колебаний, фиксируемой прибором 2. «Тяжелое место» определяется при помощи стробоскопа 4 по градуированному лимбу 5. Балансировку второго конца вала выполняют аналогично, зафиксировав опору 7 и освободив опору 9.
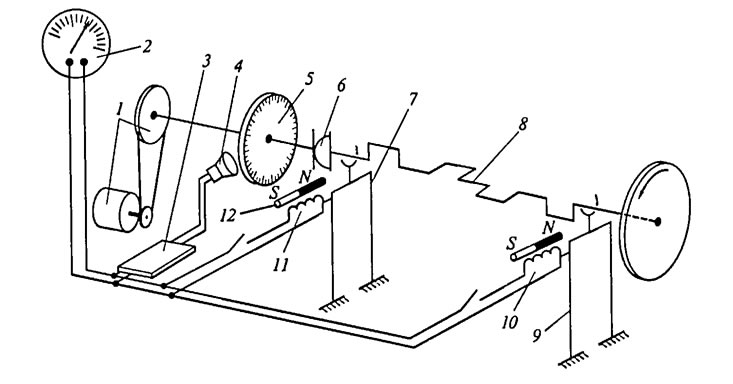
Рис. 4.22. Схема динамической балансировки коленчатого вала: 1 - привод; 2 - измерительный прибор; 3 - измерительное устройство; 4 - стробоскопическая лампа; 5 - градуированный диск; 6 - соединительная муфта; 7, 9 - упругие опоры; 8 - коленчатый вал; 10, 11 - индукционные датчики; 12 - неподвижный постоянный магнит
Устранение дисбаланса, выходящего за пределы установленной нормы для данной детали, осуществляется, как и при статической балансировке, путем удаления металла в плоскости «тяжелого места» либо посредством наплавки или приварки дополнительной пластины.