Общие требования к состоянию оборудования, применяемому при ремонте автомобилей и двигателей
Основные требования техники безопасности для различных процессов, применяемых при ремонте и восстановлении деталей, зависят от видов выполняемых работ и заключаются в следующем.
Участок разборки
Поверхность полов должна быть ровной (без порогов), гладкой, но не скользкой и удароустойчивой, не впитывающей нефтепродукты. Полы необходимо систематически очищать от смазки и грязи. Потолки и стены следует окрашивать краской светлых тонов.
Запрещается загромождать проходы, проезды и подходы к доскам с пожарными инструментами и огнетушителями Агрегаты и детали, имеющие массу более I0 кг, необходимо снимать, транспортировать и устанавливать при помощи подъемно-транспортных средств. Подтаскивание грузов краном запрещается. Разбирать агрегаты, имеющие пружины (передняя независимая подвеска, сцепление, клапанный механизм и т.п ), разрешается только на специальных стендах или при помощи приспособлений, обеспечивающих безопасную работу.
Освещенность рабочих мест искусственным светом должна соответствовать условиям работы средней точности при малом контрасте различия объекта с фоном (фон светлый) для газоразрядных ламп: комбинированное освещение — 400 лк, общее — 100 лк.
Для обеспечения электробезопасности каждое производственное помещение должно быть окольцовано шиной заземления, расположенной на высоте 0,5 м от пола и снабженной надежными контактами. Сопротивление шины заземления в любом месте не должно превышать 4 Ом. Все корпуса электродвигателей, а также металлические части оборудования, которые могут оказаться под напряжением, должны быть занулены или заземлены.
Переносной электроинструмент разрешается применять при условии его исправности при напряжении не более 36 В. Если переносной электроинструмент работает от источника энергии напряжением свыше 36 В, то он должен выдаваться вместе с защитными приспособлениями (диэлектрические перчатки, обувь, коврики и др.). Общее освещение может работать при любом напряжении, освещение станков — при 36 В, переносные лампы — 12 В. Применение ламп без арматуры запрещено. Все стационарные светильники должны быть прочно укреплены, чтобы они не давали качающихся теней.
Использованный обтирочный материал необходимо складывать в металлические ящики с крышкой. Для исключения самовозгорания ящики в конце смены следует обязательно очищать.
Моечно-очистиые работы
В процессе выполнения этих работ выделяются пары щелочных растворов, кислот, растворителей, керосина, которые вызывают раздражение дыхательных путей. Попадание ряда растворов на кожу может вызвать ожоги, а в лучшем случае — сухость кожи Вредное действие оказывает пыль, образующаяся при очистке деталей от нагара и ржавчины. Для резкого снижения влияния вредных выделений на человека применяются различные моечные машины, вытяжные устройства, защитные средства и т.п.
Моечные машины и различные установки для моечно-очистных работ оборудуются местной вентиляцией. Ванны и установки для обезжиривания растворами щелочей и растворителями должны иметь плотно закрывающиеся крышки или дверцы. Паровыводяшие трубы и установки, имеющие температуру выше 75°C, должны быть снабжены теплоизоляцией для предупреждения ожогов и уменьшения теплопотерь. Кроме местных вентиляционных отсосов на участке должна быть общеобменная приточно-вытяжная вентиляция.
Полы в помещениях должны быть ровными, гладкими, но не скользкими, а также иметь уклон для стока воды при промывке. Имеющееся на участке электрооборудование должно быть занулено и заземлено, Общее и местное освещение должно иметь пожаробезопасное исполнение.
Для защиты слизистой оболочки глаз, кожи лица и рук от «пылевого облака» и брызг раствора следует применять индивидуальные средства защиты, очки, респиратор, перчатки. Приступая к работе, мойщик должен нанести на кожу рук защитную пасту ХИОТ-6 или АВ-1 (при работе с щелочными растворами) или пасту ПМ-1 (при работе с керосином и дизельным топливом). Особую осторожность необходимо соблюдать при работе с каустической содой и ее растворами, так как попадание их на кожу вызывает ожоги. При рубке каустика необходимо надевать резиновую маску с защитными очками. Куски каустической соды можно брать только лопатами или щипцами. Запрещается применять для мойки раствор каустической соды концентрацией более 1%, а при выварочных работах — более 12%. На установках для очистки деталей в расплавах солей разрешается работать только в защитных очках с небьющимися стеклами, в брезентовых рукавицах, резиновых сапогах, комбинезоне и фартуке. Загружать соляные ванны химикатами можно при температуре нс более 250°C
Детали, подготовленные для очистки, перед загрузкой в соляную ванну обязательно выдерживают для прогрева в течение 2...3 мин над ванной во избежание выплесков расплава. При тепловых ожогах кожу необходимо промыть раствором перманганата калия (марганцовкой), смазать вазелином и перевязать При отравлении щелочами пострадавшему следует глотать кусочки льда или пить слабый раствор уксуса (0,5...1,6%), которые нейтрализуют щелочь. При ожогах щелочами пораженное место нужно промыть слабым раствором уксуса, затем водой и перевязать
Основными мероприятиями по обеспечению безопасности при работе с растворителями являются механизация и автоматизация процесса очистки. Ремонт и техническое обслуживание моечного оборудования разрешается выполнять только после отключения его электрооборудования от сети.
Сварочные и наплавочные работы
Это весьма энергонасыщенные процессы, связанные с высокими температурами, а в ряде случаев и с взрывоопасными газами, поэтому они требуют особого внимания с точки зрения техники безопасности и охраны груда.
При выполнении электросварочных работ все оборудование, находящееся под напряжением, должно быть надежно заземлено. Для защиты от ультрафиолетовых лучей и теплового излучения сварщик в обязательном порядке должен использовать защитные маски со светофильтрами, рукавицы и фартуки из несгораемой ткани К тому же для защиты окружающих от ультрафиолетовых лучей рабочее место сварщика должно находиться в специальной кабине. Она должна быть оборудована местной вытяжной вентиляцией для отсоса вредных паров, газов и аэрозолей, состоящих из оксидов металлов и продуктов сгорания обмазок и флюсов.
В качестве источников питания используют сварочные машины, трансформаторы и выпрямители. Сварочные машины рекомендуется устанавливать в отдельном помещении, а на рабочем месте в этих случаях должен быть щиток для дистанционного управления.
Рабочее место газосварщика должно быть оборудовано сварочным столом с подставкой для газосварочной горелки. На расстоянии 3...4 м от сварочного стола устанавливают рампу с кислородным и ацетиленовым редукторами и шкаф для хранения шлангов и горелок. Ацетиленовый генератор, а также баллоны с кислородом и ацетиленом хранятся в отдельных помещениях. Кислородные баллоны нельзя подвергать ударам Во избежание взрыва кислородные редукторы и вентили необходимо тщательно предохранять от загрязнения маслами и жирами.
Ацетилен с воздухом образуют взрывоопасные смеси, поэтому нужно следить за тем, чтобы не было утечки газа, и перед началом работы тщательно проветривать рабочее помещение.
Напыление металла
Этот процесс широко применяется для восстановления деталей и имеет такие же требования по технике безопасности, как при сварочных и наплавочных работах. К работам по напылению, в том числе на плазмотроне, допускаются лица в возрасте не моложе 18 лет, прошедшие медицинскую комиссию и специальный курс обучения в учебных комбинатах или ПТУ.
Наиболее сложными с точки зрения техники безопасности являются условия работы на установках для плазменного напыления, когда шум плазменной струи в непосредственной близости от плазмотрона достигает 115...120 дБ. Для зашиты оператора от шума рекомендуется наносить покрытие в специальных камерах. Воздух помещения при плазменном напылении загрязняется металлической пылью, аэрозолями обрабатываемых материалов и оксидами азота, поэтому обязательно применение местного и общего отсоса воздуха. Кроме того, плазменная струя является интенсивным источником инфракрасного и ультрафиолетового излучения, поэтому оператор должен работать в защитной маске со светофильтром. Для защиты рук от излучений применяются рукавицы из асбестовой ткани.
Гальваническое осаждение покрытий
Наиболее вредными для здоровья работающих на гальванических участках являются электролиты. Большинство кислотных и щелочных электролитов очень токсично и отрицательно действует на дыхательные пути и кожные покровы работающих. Гальванические процессы протекают, как правило, с выделением кислорода и водорода, которые увлекают за собой мельчайшие частицы электролита, насыщая воздух в помещении вредными парами.
На гальванических участках необходимо обеспечить общую приточно-вытяжную вентиляцию с 8— 10-кратным обменом воздуха в час. Наряду с этим каждая ванна с вредными выделениями должна иметь двусторонний бортовой отсос воздуха, мощность которого определяется исходя из объема воздуха, забираемого с 1 м2 поверхности ванны в час. Этот показатель зависит от состава ванны и должен быть равен, м3/ч:
- для хромирования — 6000;
- железнения — 4800;
- никелирования — 2500;
- меднения — 2000;
- электролитического обезжиривания — 3000.
При работе на гальванических участках необходимо пользоваться резиновой обувью, перчатками и фартуком. В помещении должны устанавливаться фонтанчики с водой для обмывки кожных покровов, на которые может случайно попасть электролит. Полы и стены участка должны быть покрыты керамической плиткой и ежедневно промываться. Сточные воды после промывки деталей необходимо перед спуском в канализацию пропускать через очистные сооружения.
Работа с синтетическими материалами
Участок восстановления деталей с применением синтетических материалов должен быть изолирован от других производственных помещений. Дело в том, что пластические массы в отвержденном состоянии, как правило, нетоксичны и совершенно безопасны. Однако перед отверждением отдельные компоненты, например полиэтиленполиамин, являются токсичными, и работа с ними недопустима, если процесс осуществляется не в вытяжном шкафу или не на открытом воздухе. Общая вентиляция участка должна быть приточно-вытяжной с 4 —5-кратным обменом воздуха в час. Работать с жидкими компонентами следует в резиновых перчатках, а со стеклотканью — в респираторе и защитных очках.
Аккумуляторные батареи
Работа с аккумуляторами требует соблюдения следующих правил:
- заряд батарей проводится при работающей вытяжной вентиляции;
- в помещении заряда запрещается курить и пользоваться открытым огнем;
- зарядные устройства и выключатели электрических цепей должны быть взрывобезопасными;
- полюсные выводы батарей, подготовленных к заряду, соединяют посредством плотно закрепляемых зажимов, не допускающих искрения;
- включение батарей в цепь и выключение их осуществляются только после выключения зарядного устройства;
- заряд батарей производится при открытых заливных отверстиях аккумуляторов;
- измерять напряжение аккумулятора нагрузочной вилкой разрешается только при завернутых пробках.
Нейтрализация электролита осуществляется следующим образом:
- при попадании на кожу или одежду человека промыть 10%-ным раствором питьевой соды, а затем проточной водой;
- при попадании в глаза — промыть их 2%-ным раствором питьевой соды и немедленно обратиться к врачу.
При заряде батареи происходит химическая реакция с выделением свободного водорода, который, смешиваясь с кислородом воздуха в любых пропорциях, образует гремучий газ.
На участке ремонта аккумуляторов рабочие постоянно находятся в контакте с веществами (пары свинца, серной кислоты), которые при определенных условиях или неправильном с ними обращении могут привести к травме или отравлению организма. Свинец, попадая через пищевод в кровь, оседает в печени, а серная кислота разъедает зубы и нарушает физиологические функции пищевода.
Малярные работы
При нанесении защитно-декоративных лакокрасочных покрытий на значительную часть поверхности автомобилей и их узлов эти работы выполняются в специальных окрасочных отделениях, Все такие отделения оснащаются окрасочными и сушильными камерами, необходимыми подъемно-транспортными средствами, приточно-вытяжной вентиляцией и другим оборудованием. Вентиляция помещений должна обеспечивать присутствие вредных веществ в размерах, нс превышающих допустимые санитарные нормы и взрывоопасные значения.
Обезжиривание поверхности деталей органическими растворителями типа трихлорэтилена или дихлорэтана должно производиться в закрытых аппаратах, оборудованных аппаратурой для регенерации растворителя путем перегонки, расположенной в отдельном изолированном помещении. Отработавший воздух из сушильных камер перед выпуском в атмосферу должен быть обязательно очищен.
В помещениях, где ведутся окрасочные работы, нельзя пользоваться приборами с неисправной или неприспособленной для данных условий электроарматурой, открытыми источниками огня, а также выполнять сварочные работы. В окрасочных камерах должны использоваться взрывобезопасные вентиляционные установки и переносные светильники напряжением 12 В. Запрещается работать в одной и той же камере с нитроцеллюлозными, масляными и синтетическими эмалями.
Перед окрасочными работами необходимо смазать руки защитной пастой или надеть перчатки. Для зашиты органов дыхания и зрения необходимо использовать средства индивидуальной защиты.
Смешивание лакокрасочных материалов следует производить только в краскоприготовительном отделении, а хранить их в плотно закрытой таре. Лакокрасочный материал, предназначенный для покраски окунанием, должен храниться в подземном резервуаре и подаваться насосом в ванну только на время работы Во всех отделениях (краскоприготовительных, окрасочных, на складах лакокрасочных материалов) должны обязательно находиться средства пожаротушения.
Сборочные участки
В ряде случаев эти участки являются определяющими в процессе окончательной сборки узлов и всего автомобиля. Каждый сборщик должен иметь полный набор необходимого исправного инструмента. Если, например, размер зева у какого-либо ключа превышает допустимый, то неизбежны травмы, поэтому такой инструмент должен быть исключен из пользования.
При работах на испытательных стендах оборудование должно быть надежно заземлено, а все вращающиеся части должны быть ограждены защитными приспособлениями. В помещении участка должна поддерживаться температура 18...20°C и относительная влажность воздуха в пределах 40...60%. Освещенность на рабочем месте должна соответствовать 200...500 лк.
Основные требования к оснастке, применяемой при ремонте автомобилей и двигателей
Средства технологического оснащения процессов разборки и сборки автомобилей и их узлов включают в себя технологическое оборудование, оснастку, приспособления и инструмент.
Технологическое оборудование как средство технологического оснащения предназначено прежде всего для выполнения определенной части технологических процессов по механизированной разборке и сборке агрегатов и узлов автомобилей, а также для исправления дефектов на автомобилях после ДТП и т. п.
Технологическая оснастка — это средства технологического оснащения, дополняющие технологическое оборудование, для выполнения технологического процесса по сборке, разборке и восстановлению деталей, узлов и автомобиля в целим.
Приспособления предназначены для установки или позиционирования предмета труда или инструмента при выполнении технологических операций.
Инструмент предназначен для воздействия на предмет труда с целью намеченного изменения его состояния (подробно рассматривается в следующем подразделе).
Прежде всего следует отметить, что от технологического оснащения (его конструкции, габаритов, обшей массы, удобства подхода к нему, наличия продуманных технических средств (новшеств) и т.п.) зависит, удобно ли рабочему на рабочем месте. Это, в свою очередь, повышает производительность, снижает вероятность травматизма и уровень усталости и т.д. Поэтому студенты при выполнении курсового или дипломного проекта должны уделять особое внимание этим вопросам, чтобы результат их труда соответствовал высшему уровню.
Для наглядности можно привести такой пример: в 1980-х годах японцы скупали у нас прессовое оборудование и ... сразу же отправляли на переплавку. После чего из полученного металла изготавливали новое прессовое оборудование с лучшими техническими характеристиками и продавали нам же, но в несколько раз дороже, потому что оно было более производительным, автоматизированным и удобным в эксплуатации.
Приведенный пример говорит о том, что при разработке новых устройств нужно идти с опережением существующего уровня разработок.
Механизированно-ручной инструмент
Это инструмент, главное движение которого осуществляется энергией неживой природы, а передача и управление выполняются людьми (ГОСТ 23004—78). Он включает в себя:
- инструменты общего назначения, к которым относятся сверлильные, шлифовальные, полировальные и фрезерные инструменты;
- инструменты специального назначения, к которым относятся развальцовочные, развертывающие, зенковальные и опиловочные инструменты, ножницы, кромкорезы, шаберы, пилы по металлу, клепальные и рубильные молотки, резьбозавертывающие и резьбонарезные инструменты.
Перечислим некоторые из механизированно-ручных инструментов, наиболее часто применяемых в авторемонтных процессах и их технические характеристики.
Электрические сверлильные машины с асинхронными двигателями, работающими от напряжения частотой 200 Гц, имеют массу 1,5...6,3 кг и обеспечивают сверление отверстий диаметром 6...32 мм; удельная энергоемкость — не более 40 Вт/мм.
Электрические шлифовальные машины (без гибкого вала) бывают прямые и угловые:
- прямые шлифовальные машины имеют круги диаметром 40...200 мм, рабочую скорость 50 м/с и удельную энергоемкость не более 10...16 Вт/мм. Масса инструмента 3 кг для круга диаметром 40 мм и 9 кг — для круга диаметром 200 мм;
- угловые шлифовальные машины имеют круги диаметром 125...230 мм, рабочую скорость 80 м/с и удельную энергоемкость 10 Вт/мм. Масса инструмента 6,5 кг для кругов диаметром 125 мм и 8,3 кг — для круга диаметром 230 мм.
Электрические ножницы бывают ножевые и врубные:
- ножевые обеспечивают разрезание металла толщиной 1,6...3,5 мм со скоростью 4,0...1,8 м/мин при удельном расходе энергии 143...158 Вт/мм (соответственно толщине разрезаемого металла);
- врубные обеспечивают разрезание металла такой же толщины, но с меньшей скоростью — 3,5...1,25 м/мин, при удельном расходе энергии 280 Вт/мм.
Электрические ударные гайковерты обеспечивают затяжку болтов (гаек) с диаметрами 3,6...14,9мм с энергией удара 6,3...160 Дж Они подразделяются на гайковерты без встроенного предельного (по усилию затяжки) устройства и со встроенным предельным устройством Первые имеют массу от 3 до 17 кг, вторые — в среднем на 1 кг больше. При увеличении диаметров затягиваемых болтов частота ударов снижается от четырех до одного удара за две секунды.
Пневматические сверлильные машины обеспечивают сверление отверстий с диаметрами от 6 до 32 мм (6...8, 10, 13, 16, 20 и 32 мм) при удельном расходе воздуха 2,2 (при сверлении отверстий диаметром 6 мм) и 1,2 м3/мин при сверлении отверстий диаметром 32 мм.
Пневматические шлифовальные машины подразделяются по назначению на дна вида — радиальные и торцевые:
- радиальные шлифовальные машины имеют номинальную мощность 0,03...1,7 кВт, обеспечивают обработку набором абразивного инструмента диаметром 6...200 мм при рабочей скорости 20...40 м/с. При этом удельный расход воздуха составляет от 3,0 (для круга диаметром 6 мм) до 1,3 (для диаметра 200 мм) м3/(мин·кВт); масса инструмента составляет соответственно 0,3...7,0 кг;
- торцевые шлифовальные машины имеют рабочую скорость 30...80 м/с при шлифовании абразивным инструментом с диаметром 80...230 мм, номинальную мощность привода 1,0...2,1 кВт и удельный расход воздуха в среднем от 1,4 м3/мин.
Пневматические клепальные молотки обеспечивают клепание:
- в холодном состоянии заклепок из стали 1 кп диаметром 3...10 мм при частоте ударов 38...18 с-1 и энергии ударов 2,5...22,5 Дж;
- в горячем состоянии заклепок из стали 20 диаметром 16...36 мм, при частоте ударов 18...8 с-1 и энергии ударов 22,5...70,0 Дж;
- заклепок из алюминиевых сплавов диаметром 4...8 мм при частоте ударов 38...30 с-1 и энергии ударов 2,5...12,5 Дж.
Пневматические ножницы бывают ножевые и врубные, применяются для разрезки металла толщиной 1,6...3,5 мм:
- ножевые ножницы имеют статическую силу сжатия 5...10 кгс и обеспечивают при разрезании металла производительность 3,2...1,2 м/мин при удельном расходе воздуха в пределах 0,25...0,84 м3/мин;
- врубные ножницы имеют статическую силу сжатия 2,5...3,5 кгс и разрезают металл меньшей толщины — 1,0...2,5 мм при меньшей производительности, что определяется характером процесса резания.
Оснастка
Основные требования к оснастке, применяемой при ремонте автомобилей и двигателей, заключаются в следующем.
Любая оснастка для установа агрегатов или узлов автомобиля с целью выполнения ремонтных работ должна обеспечивать закрепление их не менее чем в двух точках.
Стенды для разборочно-сборочных работ должны быть удобными для подхода рабочего и обеспечивать устойчивое положение машины, агрегата, узла или детали. С этой целью в поворотных стендах систематически проверяют исправность фиксирующих устройств, а у передвижных стендов контролируют исправность тормозных устройств.
Процесс выпрессовки и запрессовки деталей с гарантированным натягом следует выполнять только с помощью универсальных (специальных) съемников или прессов. При этом съемники должны надежно и прочно захватывать детали. Оправки необходимо строго подбирать к каждой детали.
Примеры различных видов оснастки, применяемой для ремонтно-сборочных работ, приведены на рис. 7.1—7.15.
![]() Рис. 7.1. Торцовый ключ | ![]() Рис. 7.2. Шарнирный ключ для снятия и установки свечей зажигания |
![]() Рис. 7.3. Ключ для контроля усилия затягивания свечей зажигания (с отверстием под динамометрический ключ) | ![]() Рис. 7.4. Оправка для центровки сальника валика привода масляного насоса и распределительного вала |
![]() Рис. 7.5. Съемник подшипника ведущего вала коробки передач (из торца коленчатого вала) | ![]() Рис. 7.6. Регулируемая втулка для установки нормальных и увеличенных поршней в цилиндры |
![]() Рис. 7.7. Приспособление для запрессовки поршневого пальца в поршень и шатун в горячем состоянии | ![]() Рис. 7.8. Ключ для вывертывания шпилек |
![]() Рис. 7.9. Съемник крыльчатки водяного насоса охлаждающей жидкости | ![]() Рис. 7.10. Стенд для ремонта коробки передач |
![]() Рис. 7.11 Приспособление для выпрессовки подшипников дифференциала раздаточной коробки: 1 - упор; 2 - универсальный съемник | ![]() Рис. 7.12. Съемник заднего тормозного барабана |
![]() Рис. 7.13. Съемник полуосей заднего моста | ![]() Рис. 7.14. Упор для выпрессовки внутреннего кольца подшипника дифференциала редуктора заднего моста: 1 - упор; 2 - универсальный съемник |
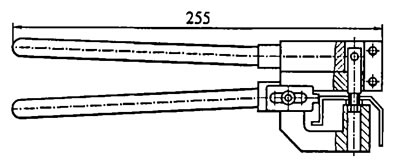
Рис. 7.15. Дырокол для пробивки отверстий в лицевых деталях кузова легковых автомобилей
Основными требованиями к технологической оснастке, применяемой при ремонте автомобилей и двигателей, является прежде всего ее целостность и отсутствие каких-либо дефектов, влияющих на ее работоспособность. Применимость этой оснастки должна своевременно проверяться контролером. При нарушении технических требований оснастка должна отправляться в ремонт или утиль.
Число единиц и номенклатура технологической оснастки на каждом рабочем месте определяются работами по технологическому процессу. Технологическое оснащение включает в себя оборудование и оснастку, измерительный, режущий, монтажный и вспомогательный инструмент. Средства технологического оснащения на рабочем месте должны размещаться в определенном, удобном для работы порядке, с тем чтобы исключить потери времени на поиски и перекладывание их с одного места на другое.
Выбор оптимальной технологической оснастки выполняется на основе решения следующих задач:
- 1) анализ конструктивных характеристик детали (габаритные размеры, материал, точность и т.п.) и технологических условий восстановления детали (схема базирования и крепления детали, вид технологической операции);
- 2) группирование технологических операций для оценки наиболее приемлемой системы технологической оснастки и повышения коэффициента ее использования;
- 3) выбор конструкции оснастки с учетом универсализации, применительно к возможному расширению номенклатуры и ускорению работ;
- 4) определение исходных требований к технологической оснастке;
- 5) отбор конструкции оснастки с учетом стандартных и типовых решений, обеспечивающих выполнение технических требований.
При технико-экономическом обосновании выбора технологической оснастки учитывают два показателя:
- коэффициент загрузки единицы технологической оснастки k3;
- затраты на оснащение технологических операций (установочно-наладочные) Су.н.о, которые вычисляются по следующим формулам:
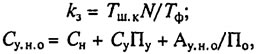
где Тш.к — штучно-калькуляционное время выполнения технологической операции; N — планируемая месячная программа на единицу оснастки (число повторений операций); Тф — имеющийся месячный фонд времени работы оснастки (станка); Сн — себестоимость изготовления сменной части (наладки); Су — затраты на установку (наладку); Пу — число установок в анализируемый период (число пусков); Ау.н.о — амортизационные отчисления за постоянную часть (установочно-наладочные); По — число наладок, закрепленных за постоянной частью (число оснащаемых операций).
Общие требования к инструменту, применяемому при ремонте автомобилей и двигателей
Ручной инструмент для слесарно-сборочных работ классифицируется по определенным группам на основе его функционального назначения, причем в пределах каждой группы имеется своя классификация.
1. Инструмент для обработки резанием: бруски шлифовальные; бруски алмазные ручные; зубила, крейцмейсели: надфили, надфили алмазные; напильники
2. Инструмент для сверления отверстий: зенкеры цельные твердосплавные; зенкеры для обработки деталей из легких сплавов; кернеры; развертки; сверла спиральные из быстрорежущей стали (короткая, средняя, длинная серии; малоразмерные); сверла спиральные твердосплавные (укороченная и нормальная серии, короткая серия, средняя серия); сверла спиральные для труднообрабатываемых материалов (короткая серия); сверла спиральные для термореактивных пластмасс; сверла перовые для обработки пластмасс из пресспорошка.
3. Инструмент для нарезания резьбы, воротки для круглых плашек, для инструмента с квадратным хвостовиком, с тремя гнездами (с шестью гнездами) и квадратным хвостовиком; раздвижные для инструмента с квадратным хвостовиком; плашки круглые для нарезания резьбы (метрическая, дюймовая коническая с углом профиля 60° и трубная коническая резьбы): метчики.
4. Инструмент для сборки резьбовых соединений: коловороты к сменным головкам; ключи гаечные с открытым зевом (односторонние, односторонние укороченные, двусторонние), гаечные кольцевые двусторонние коленчатые, для круглых шлицевых гаек, рожковые, кольцевые односторонние с четырехгранным зевом, торцовые с шестигранным углублением под ключ, шарнирные для круглых шлицевых гаек, трещоточные, гаечные торцовые, гаечные торцовые с внутренним шестигранником (односторонние, изогнутые, двусторонние), гаечные раздвижные; отвертки слесарно-монтажные.
5. Инструмент для сборки неподвижных соединений; молотки, обжимки ручные.
6. Инструмент для крепления и установки деталей: тиски слесарные с ручным приводом, тиски ручные.
7. Инструмент для резки металла: кусачки торцовые, боковые; ножницы; ножовки по металлу.
8. Вспомогательный инструмент: бородки слесарные; инструмент разметочный: циркули, чертилки; плоскогубцы (комбинированные, перестановочные, с удлиненными губками); круглогубцы; пассатижи; щипцы для сжатия и щипцы для развода пружинных колец.
Рассмотрим некоторые из инструментов, применяемых при разборке и сборке узлов и агрегатов автомобиля:
- зубила и крейцмейсели различаются по размерам и углам заточки: углы заточки зубил — 45, 60 и 70°, а крейцмейселей — 45, 60 и 70°;
- напильники (плоские, квадратные и т.п.) классифицируются по форме, номеру насечки (от 0 до 5) и длине напильника;
- надфили различаются по геометрическим параметрам и номерам насечки, а надфили алмазные — по марке алмазного порошка;
- шлифовальные бруски подразделяются по форме, геометрическим параметрам и марке шлифовальных материалов;
- сверла: если они применяются с ручной дрелью, то имеют только цилиндрический хвостовик, если с механическим приводом от шпинделя станка, то конусный хвостовик с «лапкой»;
- зенкеры предназначены для обработки отверстий, как правило, после сверления для исправления оси отверстия от увода и повышения точности;
- развертки используются для обработки призонных (точных) отверстий, при этом увод отверстия не исправляется;
- круглые плашки применяются для нарезания наружной резьбы (метрическая, трубная, дюймовая) разного диаметра и шага;
- метчиками нарезают резьбу всех размеров в сквозных и глухих отверстиях. Метчики бывают машинными и машинно-ручными. Машинно-ручные метчики изготавливают трех типов: одинарные (для всех размеров), комплектные из двух штук (для диаметров 1...52 мм), комплектные из трех штук (для диаметров 24...52 мм). Метчиками нарезают метрическую, трубную и дюймовую резьбу.
Слесарные работы дополняют или завершают механическую обработку при ремонте или восстановлении деталей автомобилей. Они незаменимы при подготовке деталей к восстановлению любыми способами. К слесарным относятся также все работы, связанные с опиловкой, подгонкой по месту, шабрением, притиркой и доводкой поверхностей для лучшего контактного прилегания деталей и пр.
При восстановлении деталей наиболее частыми являются следующие виды механической обработки: токарная, сверлильная, расточная, фрезерная, шлифовальная, полировальная, хонинговальная и др. Следовательно, наиболее ходовыми инструментами являются соответственно резцы, сверла, расточные резцы, фрезы, абразивные круги, устройства для полирования наружных, внутренних или плоских поверхностей, хонинговальные головки с абразивными брусками, настроенными на определенный диаметр, и др.
Выбор метода, вида инструмента и режима механической обработки восстанавливаемых деталей в значительной степени зависит от физико-механических свойств самой детали и примененной химико-термической обработки поверхностного слоя (цементации, нитроцементации, азотирования и т.д.).
При обработке деталей, имеющих высокую твердость, под ремонтный размер при наличии незначительного припуска применяют шлифование с заниженными режимами резания по глубине и подаче.
Наибольшие трудности возникают при обработке деталей, восстановленных наплавкой. В этом случае при твердости наплавленного металла ниже 35...40 HRC применяют токарную обработку, а при твердости выше 40 HRC — шлифование в два этапа: сначала черновое, а затем чистовое.
Трудности механической обработки напыленных покрытий обусловлены их повышенной хрупкостью, пористостью и в ряде случаев (при определенных видах материала) твердостью В зависимости от твердости покрытия и припуска обработку осуществляют точением или шлифованием. Точение напыленных покрытий осуществляют резцами из твердых сплавов на пониженных режимах: V < 60...80 м/мин; t = 0,1...0,3 мм; S = 0,1...0,3 мм/об.
Детали с напыленными износостойкими или высокотвердыми покрытиями обрабатывают шлифованием мелкозернистыми кругами на керамическом связующем (желательно алмазными кругами на вулканитовой основе) при V = 30...35 м/с, Sпрод = 0,3...0,4 мм/об и Sпопер = 0,005...0,010 мм на двойной ход стола.
При обработке деталей, восстановленных методом гальванического осаждения, например хромированием, следует учитывать, во-первых, высокую твердость наносимого электролитического хрома и, во-вторых, его незначительную толщину (при увеличении толщины слоя хрома до значений более 0,1 мм на сторону возможно отслоение наносимого покрытия). Поэтому обработка хромированных поверхностей ведется только шлифованием электрокорундовыми кругами при скорости не выше 30 м/с (Sпрод =2...10 мм/об и Sпопер = 0,002...0,005 мм) и непрерывной подаче охлаждающей жидкости не менее 25...30 л/мин. Завышение режимов приводит к образованию трещин, а также значительным остаточным напряжениям растяжения и в итоге — к резкому снижению предела выносливости детали.
При обработке пластмассовых покрытий необходимо использовать хорошо заточенный инструмент из жаростойких материалов с применением интенсивного охлаждения сжатым воздухом или керосином. Использование охлаждающих жидкостей недопустимо, так как при повышенной температуре они образуют с пластмассой соединения, отрицательно влияющие на здоровье рабочих. Рекомендуется применять для данных целей токарную обработку острозаточенным быстрорежущим инструментом при высокой скорости резания (до 250...300 м/мин) и очень малой подаче (до 0,1...0,2 мм/об).