Центральний електрод встановлений у каналі ізолятора, що має змінний діаметр. Головка електрода спирається на конічну поверхню каналу ізолятора на місці переходу від більшого діаметра до меншого. Робоча частина центрального електрода виступає на величину від 1.0 до 5.0 мм із ізолятора. Закріплення електрода в каналі ізолятора та герметизацію цієї сполуки здійснюють з використанням склогерметика. Він є сумішшю спеціального технічного скла і порошку металу. Скло повинно мати коефіцієнт термічного розширення однаковий із цим коефіцієнтом у кераміки. У цьому випадку пробка, що герметизує, не зруйнується при змінах температури в процесі експлуатації. Порошок могалла (мідь або свинець) додають у скло для надання йому електричної провідності.
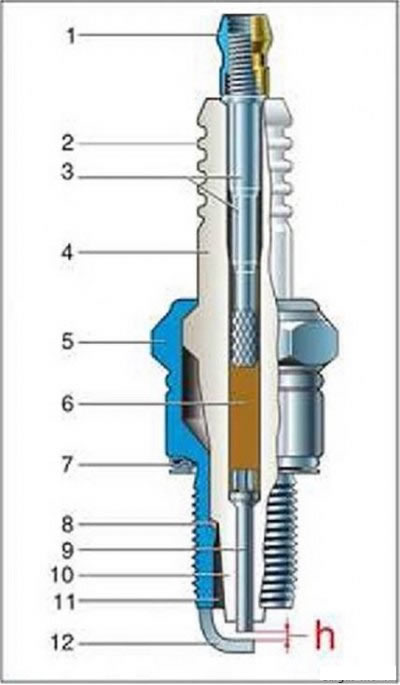
Мал. 9 - Пристрій іскрової свічки запалювання: 1 - контактна гайка: 2 - ребра ізолятора (бар'єри для струму качки): 3 - контактний стрижень: 4 - керамічний ізолятор: 5 - металевий корпус, б - пробка склогерметика. 7 - колію ущільнювача: 8 - тепловідвідна шайба: 9 - центральний електрод. 10 - тепловий конус ізолятора: 11 - робоча камера: 12 бічний електрод -маси-: h - іскровий зазор
Складання сердечника (ізолятора в зборі з центральним електродом і контактним стрижнем) здійснюють у наступному порядку. Електрод встановлюють у каналі ізолятора і зверху засипають порошкоподібний склогерметик або укладають його у вигляді таблетки. Потім канал ізолятора встановлюють контактну головку. До запресування склогерметик займає більший обсяг, ніж після цієї операції, і контактний стрижень не може повністю увійти до каналу ізолятора. Він приблизно на третину довжини виступає над ізолятором. Заготівлю нагрівають до температури 700-900 "З і з зусиллям в кілька десятків кілограмів контактний стрижень вводять про розм'якшений під впливом температури склогерметик. При цьому він затікає в зазори між каналом ізолятора, головкою центрального електрода і контактною головкою. Після остигання склогерметик обидві деталі в каналі ізолятора Між торцями електрода і контактної головки утворюється пробка, що герметизує, висотою від 1.5 до 7,0 мм, що повністю перекриває канал ізолятора від прориву газів
У разі потреби вбудувати у ланцюг центрального електрода електричний опір для придушення електромагнітних перешкод застосовують резистивний склогерметик. Після остигання герметизуюча пробка набуває електричного опору необхідної величини.
Серце встановлюють у корпусі свічки так, що він стикається своєю конічною поверхнею з відповідною поверхнею всередині корпусу. Між цими поверхнями встановлюють герметизуючу-тепловідвідну шайбу (мідну або сталеву).
Закріплення сердечника здійснюють завальцювання буртика корпусу на поясок ізолятора. Герметизацію по з'єднанню ізолятор - корпус здійснюють методом осідання корпусу в нагрітому стані (термоосадою).
Бічний електрод-маси» прямокутного перерізу приварюють до торця корпусу і згинають у бік центрального. На цоколь корпусу з упором в плоску опорну поверхню встановлюють кільце ущільнювача, призначене для герметизації з'єднання свічка - двигун.
На різьбову частину контактного стрижня встановлюють контактну гайку, якщо це потрібно конструкцією високовольтного наконечника проводу. У деяких свічках контактний стрижень немає різьбової головки, вона відразу ж штампується у вигляді контактної гайки.
Ізолятор
Для забезпечення безперебійності іскроутворення ізолятор повинен мати необхідну електричну міцність навіть за високої робочої температури. Напруга, що прикладається до ізолятора в процесі роботи двигуна, дорівнює напрузі пробою іскрового зазору. Ця напруга зростає зі збільшенням тиску та величини зазору та зменшується у міру зростання температури. На двигунах із класичною системою запалювання використовуються свічки із іскровим зазором 0.5-0,7 мм. Максимальна величина напруги пробою в умовах не перевищує 12-15 кВ (амплітудне значення). На двигунах з електронними системами запалювання настановний іскровий зазор становить 0,8-1,0 мм. У процесі експлуатації може збільшитися до 1,3-1,5 мм (в обох систем). При цьому напруга пробою може досягати 20-25 кВ.
Конструкція ізолятора відносно проста - це циліндр із осьовим отвором для встановлення центрального електрода.
в середній частині ізолятора є потовщення, так званий - поясок - для з'єднання з корпусом. Нижче пояска розташована тонша циліндрична частина -дульце, що переходить в тепловий конус. У місці переходу від дульця до теплового конуса розташована конічна поверхня, призначена для встановлення між ізолятором і корпусом шайби, що герметизує тепловідвідну. Вище пояска розташована -головка', а в місці переходу від пояска до головки розташоване плічко під завальцювання буртика корпусу при складанні свічки.
Допустима, з урахуванням коефіцієнта запасу міцності, товщина стінок визначається електричною міцністю матеріалу ізолятора. За вітчизняними стандартами ізолятор повинен витримувати випробувальну напругу від 18 до 22 кВ (діюче значення), що більше амплітудного в 1.4 рази. Довжина головки ізолятора визначається напругою поверхневого перекриття та виконується в межах від 15 до 35 мм. Більшість автомобільних свічок ця величина близько 25 мм. Подальше збільшення малоефективне та призводить до зниження механічної міцності ізолятора. Для виключення можливості електричного пробою по поверхні ізолятора його головку постачають кільцевими канавками (бар'єрами струму) та покривають спеціальною глазур'ю для захисту від можливого забруднення.
Функцію захисту від поверхневого перекриття камери згоряння виконує тепловий конус. Ця найважливіша частина ізолятора при відносно невеликих розмірах витримує без перекриття поверхнею зазначену вище напругу.
Спочатку як матеріал ізолятора застосовували звичайний фарфор. але такий ізолятор погано чинив опір тепловому впливу і мав низьку механічну міцність.
Зі збільшенням потужності двигунів були потрібні ізолятори більш надійні. ніж порцелянові. Довгий час застосовували слюдяні ізолятори. Однак при використанні палив із присадкою свинцю слюда руйнувалася. Ізолятори знову почали виготовляти керамічними, але не з порцеляни, а з особливо міцної технічної кераміки.
Найбільш поширеною та економічно доцільною для виробництва ізоляторів є технологія ізостатичного пресування, коли із заздалегідь підготовлених компонентів виготовляють гранули необхідного складу та фізичних властивостей. З гранул при високому тиску пресують заготівлі ізоляторів, шліфують до необхідних розмірів з урахуванням усадки при випаленні, а потім випалюють одноразово.
Сучасні ізолятори виготовляють із високоглиноземистої конструкційної кераміки на основі оксиду алюмінію. Така кераміка, що містить близько 95% оксиду алюмінію, здатна витримати температуру до 1600 'З має високу електричну і механічну міцність.
Найважливішою перевагою кераміки з оксиду алюмінію є те, що вона має високу теплопровідність. Це суттєво покращує теплову характеристику свічки, оскільки через ізолятор проходить основний потік тепла, що надходить у свічку через тепловий конус та центральний електрод (рис. 10).
Корпус
Металевий корпус призначений для встановлення свічки в двигун та забезпечує герметичність з'єднання з ізолятором. До його торця приварюється бічний електрод, а в конструкціях з кільцевим іскровим проміжком корпус безпосередньо виконує функцію електрода «маси».
Корпус виготовляють штампуванням або точенням із конструкційних маловуглецевих сталей.
всередині корпусу є кільцевий виступ із конічною поверхнею. на яку спирається ізолятор. На циліндричній частині корпусу виконана кільцева проточка, так звана термоосадова канавка. У процесі збирання свічки верхній буртик корпусу завальцьовують на поясок ізолятора. Потім його нагрівають і осаджують на пресі, при цьому термоосадова канавка піддається пластичній деформації, корпус щільно охоплює ізолятор. В результаті термоопаду корпус виявляється в напруженому стані, що забезпечує герметичність свічки на весь термін служби.
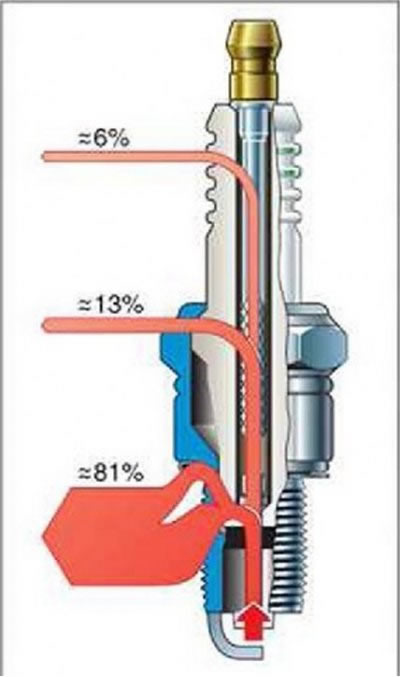
Мал. 10. Теплові потоки в ізоляторі свічки
Електроди
Як сказано вище, для поліпшення ефективності займання електроди свічки повинні бути якомога тоншими і довгими, а іскровий зазор повинен мати максимально допустиму величину. З іншого боку, для забезпечення довговічності електроди мають бути досить потужними.
Тому, залежно від вимог до потужності, паливної економічності та токсичності двигунів, з одного боку, та вимог до довговічності свічки з іншого боку, до кожного типу двигуна розроблялася своя конструкція електродів.
Поява біметалічних електродів дозволила певною мірою вирішити цю проблему, оскільки такий електрод має достатню теплопровідність. На відміну від звичайного «монометалевого» він при роботі на двигуні має меншу температуру і відповідно більший ресурс. У тих випадках, коли потрібно збільшити ресурс, застосовують два електроди "маси-" (рис.11). На свічках зарубіжного виробництва з цією метою застосовують три і навіть чотири електроди. Вітчизняна промисловість випускає свічки з такою кількістю електродів тільки для авіаційних та промислових газових двигунів Слід зазначити, що зі збільшенням числа електродів знижується стійкість до утворення нагару та утруднюється очищення від нагару.
До матеріалу електродів пред'являються такі вимоги: висока корозійна та ерозійна стійкість: жаростійкість та окалиностійкість: висока теплопровідність; достатня для штампування пластичність. Вартість матеріалу не повинна бути високою Найбільшого поширення у вітчизняній промисловості для виготовлення центральних електродів свічок запалювання отримали жаростійкі сплави: залізо-хромтитан, нікель-хром-залізо та нікельхром з різними легуючими добавками
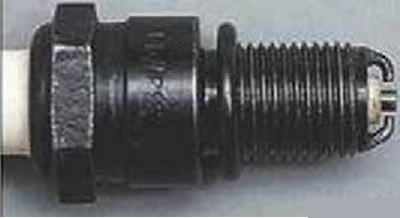
Мал. 11. Свічка А26ДВ-1 з двома бічними електродами маси
Бічний електрод «маси» повинен мати високу жаростійкість і стійкість до корозії. Він повинен мати гарну зварюваність із звичайною конструкційною сталлю, з якої виготовляють корпус, тому застосовують сплав нікель - марганець (наприклад. НМц-5). Бічний електрод повинен мати гарну пластичність для забезпечення можливості регулювання іскрового зазору.
З метою зниження впливу електродів, що гасить, при доробці свічок на електродах виконують канавки, в електроді -маси» виконують наскрізні отвори. Іноді бічний електрод поділяють на дві частини, перетворюючи одноелектродну свічку на двоелектродну.
Вбудований резистор
Іскровий розряд є джерелом електромагнітних перешкод, у тому числі радіоприймання. Для їх пригнічення між центральним електродом і контактною головкою встановлюють резистор, що має при температурі 25±10°С електричний опір від 4 до 13 кОм. У процесі експлуатації допускається зміна величини цього опору в діапазоні 2-50 кОм після дії температури від -40 до +300°З імпульсів високої напруги.
Додатковий ізолятор
Навіть невеликі втрати енергії запалення призводять до ослаблення іскри з усіма неприємними наслідками: погіршення пуску, нестійка робота на холостому ходу, втрата потужності двигуна, перевитрата палива, зростання токсичності газів, що відпрацювали і т. д. Якщо поверхня ізолятора покрита нагаром, брудом або просто волою відбувається витік струму "на масу". Вона виявляється у темряві як коронного розряду на поверхні ізолятора. Витік забрудненої поверхні теплового конуса ізолятора в камері згоряння двигуна може призвести до відмови в іскроутворенні. Найбільш радикальним способом підвищення електричної міцності ізоляції є встановлення між корпусом та контактною головкою свічки додаткового ізолятора у вигляді керамічної втулки. Таким чином, свічка набуває подвійного захисту від витоків струму «на масу».
Форкамерні свічки
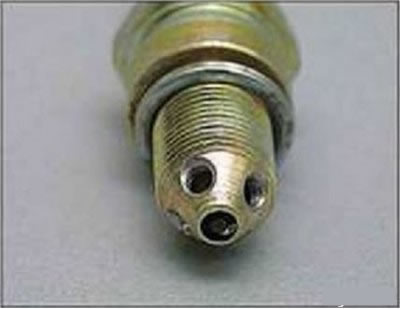
Мал. 12. Форкамерна свічка запалювання
Відомі різні варіанти влаштування свічки, у яких робоча камера виконана у вигляді форкамери. Їх використовують з метою покращення згоряння робочої суміші. Форкамерні свічки подібні до свічок для спортивних форсованих двигунів, де електроди для захисту від перегріву встановлені глибоко всередині робочої камери корпусу. Відмінність у тому. що отвір. що з'єднує робочу камеру (форкамеру) з циліндром двигуна, роблять спеціальні форми. При стисканні свіжа суміш надходить у форкамеру, іскровий розряд виникає в області вихрового потоку, і утворення первинного вогнища займання стає інтенсивнішим. Завдяки цьому забезпечується швидке поширення полум'я у форкамері. Тиск швидко зростає і викидає смолоскип полум'я, що проникає в камеру згоряння двигуна і інтенсифікує займання навіть сильно збідненої робочої суміші.
При перетіканні газів з форкамери в циліндр двигуна, у зв'язку з турбулізацією горючої суміші, прискорюється і стає більш ефективним процес згоряння. Це. у свою чергу, може призвести до поліпшення показників, що характеризують паливну економічність і токсичність газів, що відпрацювали.
Недоліки форкамерних свічок полягають у тому, що великий вплив електродів, що гасить, а стійкість до утворення нагару мала. Вентиляція форкамери утруднена і горюча суміш містить підвищену кількість залишкових газів. При перетіканні газів з форкамери в циліндр виникають додаткові теплові втрати. Один із варіантів форкамерної свічки представлений на рис. 12